BACKGROUND
Steel debris, when allowed to remain on a building following its construction, will quickly rust, causing an unsightly stain that is difficult to remove. To the untrained eye, steel debris looks like premature corrosion. As a result of the appearance, the owner of the building may become understandably upset, believing the contractor used inferior materials that have little or no corrosion protection.
Steel debris includes iron fines left from cutting and/or drilling operations when using friction saws, abrasive discs, drills, etc. Additionally, weld splatter from welding operations may also contribute to steel debris. Steel debris may include other construction materials left on the roof, such as nails, screws, staples, nuts, rivet shanks, etc.
Prevention of steel debris staining is the responsibility of the installer. Materials suppliers will not accept claims for it. Stain prevention is much easier and less expensive than cleaning and repairing the stain caused by the steel debris. In severe cases, such staining can lead to replacement of the panels.
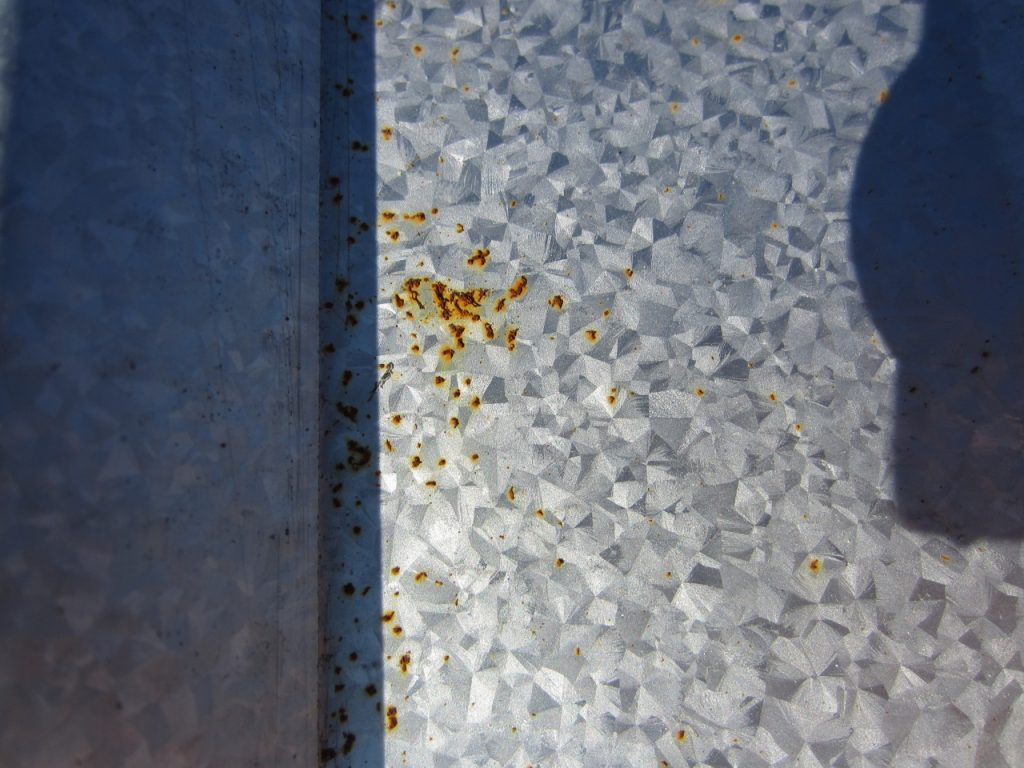
WHAT DOES STEEL DEBRIS STAIN LOOK LIKE?
Fresh steel debris stains are small red-brown colored spots with a central dark spot (the remains of the steel particle). Steel corrosion eliminates fine steel debris within a couple of years on painted panels. The stain will remain long after the metallic iron has rusted away. The panel feels rough from loose or embedded particles. On bare panels, galvanic action protects the debris, possibly depleting the metallic coating in the immediate vicinity. An old steel debris stain will appear as a smoother surface with a localized red-brown stain in the area where the steel particle corroded away. Iron fines from drilling cause groups of stain spots around the hole. Cutting often causes a line of stain spots along the cut. Tracked particles cause randomly dispersed spots on the roof. Inadequate washing moves particles to the inside of the profile.
PREVENTING
STEEL DEBRIS STAIN
There are four steps to preventing steel debris staining. The best method is to not form the iron fines in the first place. When this is not possible, the exposed surface should be protected from debris generated during cutting, drilling or welding. Additionally, the panels need to be protected against tracking. Finally, all debris should be cleaned off the panels.
Preventing Steel Debris Stain — Cutting
Where possible, minimize cutting by using factory supplied cut-to-length sheets. The custom shears used by the factory to cut the profiles to length leave no debris on the sheet.
To prevent formation of steel fines, the best tools for on-site cutting are profile shears, hand shears, or electric nibblers. Because these methods form a smooth edge, they are the only acceptable cutting methods with respect to corrosion of exposed edges. Rechargeable or plug-in hand-held electric nibblers easily cut standard panels. Hand shears may not be suitable for longer cuts, but may be useful when multiple layers of steel require cutting.
A power saw with a metal cutting steel blade is the next best way to cut sheets on-site. Power saws generate larger and cooler particles than abrasive discs. The particles are thus less likely to burn into a painted surface. If material needs to be cut near installed sheets, mask the area near the cut to keep the hot particles away from the completed work.
If on-site cutting is necessary, cutting on the ground keeps steel particles away from other panels. Facing the exterior color finish of the prepainted steel down prevents steel particles from landing on the exterior surface. Take care to ensure that hot steel particles do not come into contact with prepainted steel sheets and DO NOT cut above other coated products, where debris may fall onto other sheets.
Preventing Steel Debris Stain — Welding
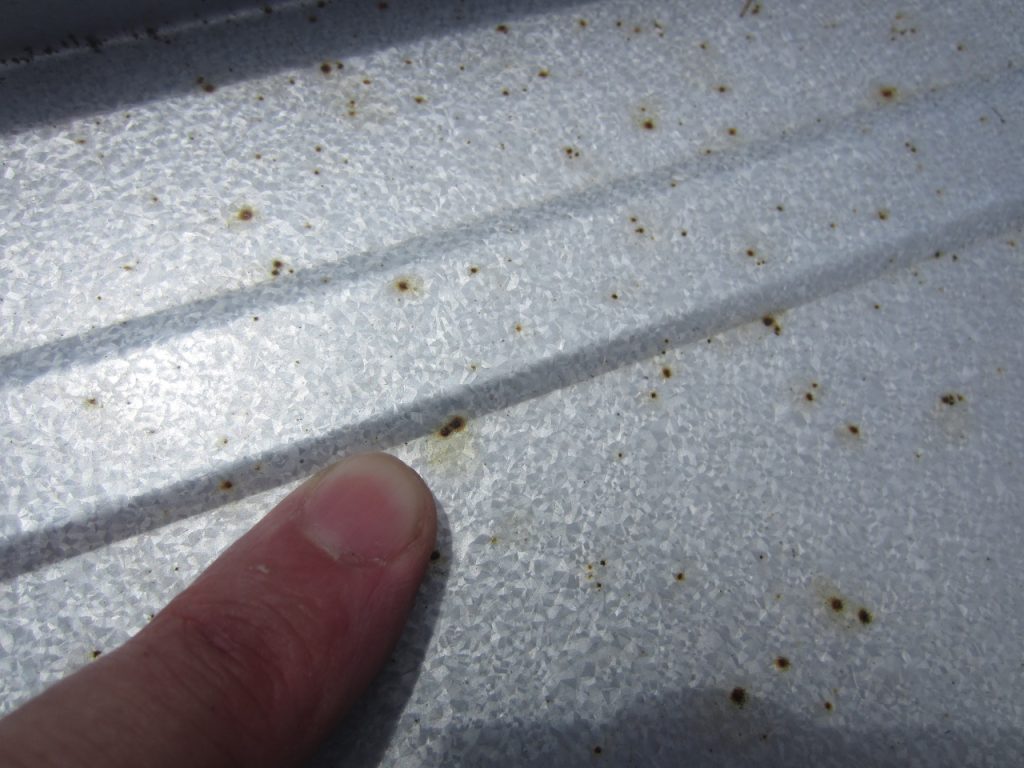
Unlike fines from cutting and drilling, weld splatter is much more likely to burn through the paint to the metal surface. This is also likely to be a problem with bare metal. If possible, avoid welding on or near building panels. When welding is necessary, mask the surrounding area with scrap metal to prevent the splatter from hitting panel surfaces.
Preventing Steel Debris Stain — Fastener Holes
The best method for making a fastener hole is to start it with a punch and then to use a self-tapping screw. To prevent bending the panel, make the hole using a backer. Punching holes will not leave fines, but may create an inside burr. Using a punch works best on a wood frame.
There are circumstances when punching a hole is not practical. In these cases, drilling should be conducted on the ground in the manner described above for cutting. If drilling holes on the building is unavoidable, mask the area around the hole to shield the panel from hot metal.
Always use sharp drill bits to reduce the formation of steel fines. Dull bits form smaller, hotter steel particles that are more likely to melt into the paint. Sharper bits will often form easily removed spirals.
Preventing Steel Debris Stain — Clean-up
Sweep or hose the steel particles from the job as the job progresses to remove loose particles and particles not well embedded in the paint. Take great care to avoid any action that is likely to remove the paint or metal when attempting to detach embedded debris. Any damage to these coatings will lead to a reduced life of the material.
Clean the debris from the panel progressively or at least at the end of each day. When sweeping or hosing into a gutter, clean it out before leaving the job in order to prevent premature corrosion of the gutter. Upon completion, give the job a final wash. Manually remove larger pieces, such as nails and screws, not washed off as part of the final clean-up.
For critical applications or bare metal, inspect the job after two weeks. Rain or condensation will cause the remaining steel particles to rust, highlighting affected areas. On bare roofs, steel particles not removed can become a serious corrosion problem.
Preventing Steel Debris Stain — Tracking
All construction sites generate steel particles on the ground. Construction crews can track these particles onto the roof or panels on the ground from the soles of their shoes.
Bare GALVALUME®1 Coated Sheet Steel or HDG coated sheet steel roofs are subject to staining from tracking of dirt and other construction area soils onto the roof. Painted panels can become scratched or marred when the soles of shoes grind soils or steel debris into the paint surface.
Ribbed or soft soles carry the particles easier than smooth or hard-soled shoes. One possible solution would be to use slip-on shoe covers to wear on the finished surface. This would ensure no debris being tracked on the roof. Any worker that walks on a new roof panel should take precautions not to transfer dirt or steel debris to the fresh surface.
Another solution is for the roofing workers not to switch to the ground and back. Once the crew is on the roof, the workers on the ground should send up all materials needed rather than the roof crew retrieving them. The workers on the roof should remove the dirt and debris on the soles of their shoes.
Architects and general contractors need to know about the problems arising from tracking of steel debris. They must then warn the appropriate supervisors so that they discuss the necessary precautions with all workers at the site. Precautions against panels on the ground being walked on is necessary for construction site visitors.
EFFECT OF STEEL DEBRIS ON PANEL CORROSION
The main effect of steel particle staining on painted panels is aesthetic. It is usually not detrimental to the overall corrosion performance. Typically, paint separates the debris from the metallic coating. It forms red rust until completely rusted away. The natural weathering action will deplete the red stain on top of the paint.
Only rarely, will steel particles penetrate the paint and contact the protective metallic coating. The red rust is inert, but steel particles in contact with the coating will accelerate zinc corrosion, leading to premature coating depletion and paint peeling.
On bare metal coating, steel debris will cause accelerated corrosion in a small area. The zinc in the coating sacrifices itself to prevent oxidation of both the steel debris and any exposed areas of the base steel. This leads to premature coating failure and a shorter panel life. Any cleaning that does not remove the steel particles will not help the coating.
LEAVING THE DEBRIS AND STAIN
Leaving the stain and debris on bare metal roofs is not an option. Failure to remove the particles quickly will lead to galvanic attack of the coating and possible premature perforation of the panel.
In virtually all circumstances, the stain on painted panels is only a cosmetic imperfection. Not cleaning the stain is a viable option. Removing the stain after a couple of years’ exposure is easier than removing it immediately. The steel particles embedded in the paint will corrode away in that time. Any steel particles that remain after cleaning will rust again, causing more stain.
On paints that chalk, natural washing action will remove the stain. On paints that do not chalk, such as fluorocarbons, the stain will remain for a very long time if not cleaned.
REMOVING THE STAIN — BARE STEEL SHEET
Brush the surface with a bristle (not metallic wire) brush to dislodge particles. Completely remove them by washing the dislodged particles off the building. Leaving the particles in the gutter could reduce the life of the gutter. Wire brushing can change the panel’s appearance and could remove some of the metallic coating. If corrosion from the debris severely damages the metallic coating, affected areas may require painting to obtain the desired protection. Do not use any kind of steel wool as it will break up and create steel particles. Any steel particles that remain after cleaning will cause further stain.
REMOVING THE STAIN —PREPAINTED STEEL SHEET
Completely remove the steel debris, through natural corrosion of the particles or through mechanical methods. Permanently remove the stain with a recommended cleaner.
A mild abrasive cleaner, applied lightly with a non-abrasive pad, can remove normal staining and most of the particles causing the stain. It is necessary to only use light pressure as the cleaner may remove the paint and will affect the paint gloss. Do not use steel wool.
More severe staining requires extensive cleaning. There will be more particles and more rust. In this situation, use a nylon brush or a non-marring abrasive pad to remove embedded steel particles. Test any cleaning procedure on a non-exposed section to ensure it will not remove the paint. The abrasion will probably lower the surface gloss.
Sandpaper or nylon abrasive pads (not steel wool) are acceptable for removing difficult steel debris when repainting an area. Since this also removes most of the rust staining, subsequent washing with a mild abrasive cleaner or another recommended cleaner will remove the remaining rust. Otherwise, follow the standard procedures for repair painting specified by the paint supplier. Never use strong acids or alkalis.
Paint blistering in the immediate vicinity of a stain indicates penetration by the steel debris. This penetration is very rare, but the corrosion causing the blistering will continue if not removed.
SUMMARY
1. Steel debris from cutting, welding, and drilling or steel debris from small pieces, such as nails, will cause red rust stain spots on painted or bare panels.
2. To avoid staining: do not form steel particles; if the steel particles are formed, keep the particles off the panel surface and clean off those particles that get on the panel as soon as practical.
3. Make fastener holes without drilling by punching holes. Make cuts without much debris by using an electric nibbler or profile shear.
4. Drilling or cutting on the ground keeps the fines off the building. If the exposed side is down, the particles stay off the exterior paint.
5. Mild abrasive cleaning will remove the stain and most of the particles, but any remaining steel particles will cause the stain to return. MR