By Tracy Schubert
Contractors know the terms HOA, permit and zoning very well. Customers count on installers to network and follow the rules adopted in their best interests. It’s important to have a good understanding of what can be built before materials are ordered in an HOA-involved situation. No one can afford to have money tied up in unusable, delivered inventory.
Becoming a go-to contractor within a growing HOA can be a great business advantage. Creating a strong group of customer referrals within an HOA will help you network to other HOA clients and demonstrates your ability to get things done. Word of mouth about quality of workmanship, materials used, and the ability to complete jobs on time pays off in jobs gained.
Homeowner’s Association requirements known as covenants, conditions and restrictions (CC&Rs) function as the rules agreed to within the community. Obtaining a copy of those CC&Rs before doing any work is important. There can be rules about what materials and colors are allowed for roof.
If there are rules for the HOA, and what your client wants to select is not on the pre-approved list, permission must be obtained. The person contracted to pursue the approval, the contractor or the client, will need to find out what forms must be filled out to get said approval and when they are due to make the agenda for the next meeting, since HOA’s often only meet once a month. Find out what samples and plans you may be required to submit for approval and how long it will take for the HOA to decide about your proposal. Timeline impacts are significant for both you and your client to understand because they may impact the materials they are considering. The time involved to step out of the HOA CC&Rs might not be worth the impact to the project. Also important to remember: HOAs need work done to maintain areas of common interest within the community.
Zoning requirements can contain pretty specific detail and are something to keep current on to avoid corrective delays during inspections. Some of the standards are based on old thinking and may surprise builders familiar with current industry thinking so adjustments may need to be requested. Building codes are updated by the ICC every three years, but those recommendations do not always trickle down to all localities. Again, time considerations that can negatively impact a project and ending up with unusable materials that have to be removed for not being in code benefit no one.
The following list contains the 2021 metal roofing requirements in a northern Wisconsin city. There are some very specific exclusions and required use elements:
• Metal shingles that mimic traditional roofing products such as clay tile and wood shakes will be permitted.
• Architectural flat panel standing seam or flat panel batten systems are required; corrugated panels are not allowed.
• Concealed fasteners are required; exposed fasteners are not permitted. (WMC 23.70.10(4)(c)(1))
• Mechanically attached snow guards are required (multiple systems are available) to prevent or minimize snow and ice slides around perimeters and all eaves. Consideration shall be given to protection of utilities (away from gas meters, vents dryer, furnace, hot water heater, other gas appliances, etc.).
• Metal to be either intrinsically weather-resistant (copper, zinc, terne, or other known metals) or coated with factory applied, proven anticorrosion coatings/paints.
• Colors must be earth tones or compatible with colors of traditional roofing products with a Kynar or equivalent fade-resistant coating, or base metal if exposed weather-resistant metals are used.
• All old roofing materials must be removed and the metal roof installed in accordance with manufacturer specifications. A minimum 15-pound roofing felt shall be used as required by the Uniform Dwelling Code.
In this particular city, it is good to make sure your client understands that snow guards are required and what options are available. There will be cost impacts to the job because of these requirements.
This city allows for manufacturer specifications to be used for the installation but requires all old roofing materials be removed. That is not always needed for an environmentally friendly installation of a metal roof and is also an additional expense to be considered. There are color requirements in this city for earth tones or compatibility with colors of traditional roofing products with a Kynar or equivalent fade-resistant coating, or base metal. Very important to make sure the desired look is considered to adhere to those requirements if you are considering a bright lipstick red roof, cobalt blue or a purple mica/metallic paint.
Make sure to have a clear understanding with your client about who is obtaining any needed permits and who is scheduling inspections. Building permits are authorizations issued by a city or county and often reflect regional needs, such as fireproofing, heat and humidity. They are also needed for special system permits, like plumbing and electrical work. Find out what is needed by contacting the local office and checking for information online.
Demonstrating adept knowledge of HOA requirements, zoning and permit pulling areas in tandem with using quality materials, being licensed and insured and having a catalog of happy customers and truly fair, detailed contracts will put you a step above others bidding a job.
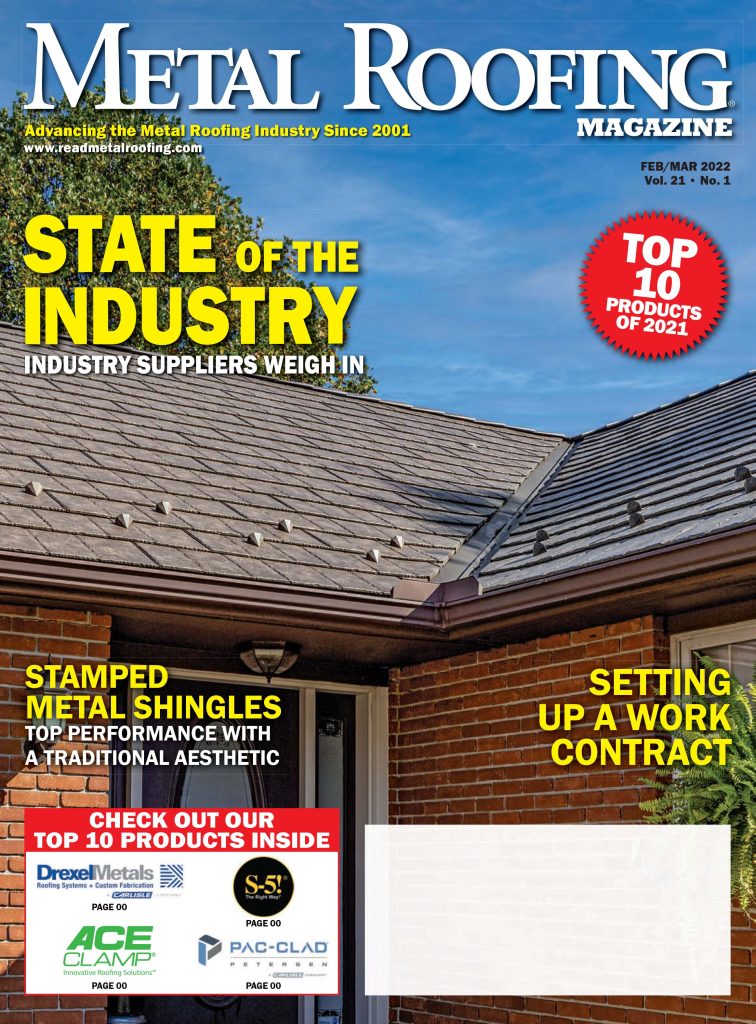
Sign Up For A Free Subscription
Anyone who is involved in the construction trade is welcome to sign up for a free print or digital subscription to Metal Roofing Magazine, which has been advancing the metal roofing industry since 2001. This go-to resource for metal roofing professionals is published 7 times per year.