Editor’s Note: This technical bulletin was published by the Metal Construction Association [www.metalconstruction.org], and is reprinted with permission.
Profiled metal roof or wall panels rely upon mechanical fasteners to secure the components to a structure. It is very important to select the correct type of fastener for metal construction in order to ensure a strong and weather-tight attachment. This Technical Bulletin serves as a guide for the selection of exposed fasteners used with metal roof and wall panels.
Discussion
Fasteners are either primary or secondary in nature. Primary fasteners are used to transfer loads from one design element to another. These loads can be dead, design, imposed and wind loads. Where used externally, these fasteners must provide a weather-tight seal under all load conditions. They are also often required to be coated or colored in some way to match the material they are securing.
There are many different types of fasteners. These fastener types include “self-drilling,” “self-tapping,” or both. Self-drilling (SD) screws have a drill point in the tip of the fastener. Self-tapping (ST) screws do not have a drill point but are able to tap their own threads into the attachment material. Self-piercing (SP) screws “pierce” through light gauge metals then self-tap (ST) into the material below.
For example, type A, B or AB screws are self-tapping. The fasteners commonly used for attaching to light gage framing are self-drilling self-tapping screws (SDST). These threaded fasteners have the ability to drill their own hole and form their own internal mating threads. Another type of tapping screw can be “self-piercing,” which has the ability to pierce metallic material 33 mils (0.033”) or less in thickness and tap their own mating threads when driven. Self-piercing tapping screws have a sharp point angle not more than 30 degrees and are often used to secure metal panels to wood substrates.
Durability
Secondary fasteners must maintain a secure attachment. They can be used to provide lateral resistance such as part of a diaphragm. They are typically used for stitching of sidewall and roofing laps or securing flashing or other components to sheeting. These types of fasteners are often used with sealants or washers to draw the joint tight. Secondary fasteners may be coated or colored to match the surrounding material. Examples of these types of fasteners may be self-drilling or self-tapping screws, or rivet type products.
Any type of fastener must be designed to be as durable as the metal wall or roof cladding system itself. Fasteners are available in a variety of substrates and materials with different levels of corrosion resistance and/or durability when exposed to the harsh conditions of weather for years. The metal roof or wall panel manufacturers can provide specific recommendations for selecting fasteners for a specific system.
Compatibility
A potential risk to the integrity and aesthetics of a building exists when the wrong type of fastener is used with a metal roof or wall cladding system. Under certain conditions, premature corrosion of the metal panel and/or the fastener may occur. This effect is known as galvanic corrosion and is often a result of corrosion between the dissimilar metals that are in contact with each other. When selecting fasteners, the relative surface area of the contact points as well as the acidity of the rainfall in the environment need to be considered.
To prevent dissimilar metal corrosion at the connection point, fasteners should be made of the same material as the roof or wall systems whenever possible. At the very least, the fastener should display equivalent corrosion resistance to the material being fastened into. As an example, the use of galvanized steel fasteners with aluminum metal wall cladding systems is not recommended.
To assist designers and installers with the selection of proper fastener types, the table shown on page 24 was developed by the Metal Construction Association to serve as a guideline for compatibility with different types of materials. The intent is to show equivalent corrosion resistance between the fasteners and cladding material.
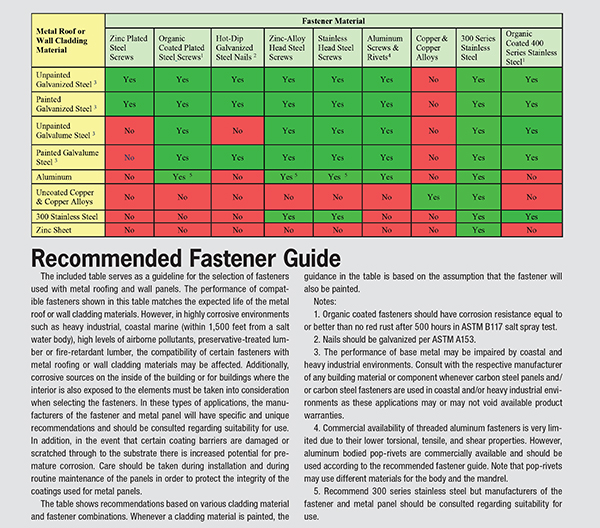
Load Resistance
Fasteners of any type or material are used to resist an applied load. Some connections are critical components in the structural design of the building while others are not. When an attachment involves design critical elements, the use and frequency of any fastening device shall be considered carefully and proven by testing and/or engineering analysis.
SPECIAL NOTE A: Use of Seam Clamps and Brackets
It is common practice to utilize aluminum seam clamps (for standing seam profiles) and specialty brackets (for face-attached profiles) to facilitate the attachment of rooftop ancillaries such as service walkways, solar collectors, snow retention devices and other roof accessories. Seam clamps pinch the seam by some mechanical means, but without penetrating the seam material. In such applications, aluminum clamps are suitable for use with all cladding types tabled with the exception of “Copper and Copper Alloys,” provided that accompanying hardware is 300 series stainless steel. Stainless setscrews or other nodes that engage the cladding material should have rounded tips so as not to abrade metallic coatings on steel, or cause fracture points to other metals listed. Avoid sharp edges or points on fasteners or clamps engaging the seam.
Specialty brackets for use on face-attached cladding profiles when constructed of aluminum are suitable for use with all cladding types in the table with the exception of “Copper and Copper Alloys.” Screws or bolts that attach these brackets should be selected in accordance with the guide table.
SPECIAL NOTE B: Preservative-Treated Lumber Applications
Preservative-treated lumber can be incompatible with certain types of fasteners. In those cases where any type of metal roof or wall cladding materials are being attached to preservative treated lumber, the following fasteners are not compatible: zinc plated screws, zinc-alloy headed screws, stainless capped screws, and aluminum. When attaching metal panels to preservative-treated lumber, a moisture barrier may be used between the lumber and the panel material. Metal panel fasteners that are compatible with preservative-treated lumber are stainless steel fasteners, or hot dip galvanized nails manufactured to ASTM A153 Class D or heavier. Other types of fasteners coated with proprietary anti-corrosive technologies are also available for use with preservative-treated lumber.
• Copper fasteners may be used with preservative treated wood as allowed by code.
• If panels are coated on both sides, a moisture barrier may not be needed.
• Zinc plated fasteners and bolts should not be used with any preservative treated wood. Especially with waterborne treatments.
About the Metal Construction Association
Founded in 1983, the Metal Construction Association [www.metalconstruction.org] brings together the diverse metal construction industry for the purpose of expanding the use of all metals used in construction. MCA promotes the benefits of metal in construction through:
• Technical guidance and product certification.
• Educational and awareness programs.
• Recognition of industry-achievement awards
• Monitoring of industry issues, such as codes and standards.
• Research to develop improved metal construction products.
• Promotional support for the industry.
• Publications to promote use of metal products. MR