By Jessica Franchuk
Information Provided by Sherwin-Williams Coil Coatings, AkzoNobel, and PPG Industrial Coatings
It’s a simple fact—every roof that is installed will be impacted by external factors—with weather and sun exposure at the top of the list. Of course, the impact of the region’s specific weather varies greatly depending upon the location of the roofing project. Drew Waldroup, Account Manager for Sherwin-Williams Coil Coatings, explained: “This is because the coatings must be formulated with the local environment at top of mind. Is it a northern climate with excessive thermal variations? Is it in a coastal zone and subject to salt spray? The right coating formulation is of great importance to coating performance.”
Standard Testing Processes
In order for coatings manufacturers to know how their products will perform over time when exposed to the elements, they must follow a testing procedure. Sherwin-Williams Coil Coatings conducts their own weather testing, which has become critical in preventing product failures.
Innovation matters to the company, which continues to improve the performance and durability of their coating systems through research and development: “A well-planned weathering test program could identify coating failure risks in advance. With this, new formulations are created and need to be tested to failure.” From their Weatherability Matters literature, the potential failures they test for include:
• Gloss Retention:
Gloss refers to a coating’s ability to reflect light without it scattering. Direct UV exposure can degrade the luster of the topcoat. While all types of coatings will lose some degree of gloss over time, lower quality paints will generally lose gloss much earlier than superior coatings.
• Chalking:
Chalking is caused by degradation of the resin system at the surface of the finish due to exposure to UV rays. As the resin system breaks down, resin particles take on a white appearance and embedded pigment particles lose their adhesion to the film. Chalking is tested by transferring the chalk to fabric or adhesive tape, then comparing it to a photographic reference standard (ASTM D4214 Standard Test Methods of Evaluating the Degree of Chalking of Exterior Paint Films). The range is from 10 to 1, with 10 showing the least amount of chalking and 1 showing the presence of extreme chalking.
• Fading/Delta E:
Delta E (dE) is a single number that represents the distance between two colors. One color is always the standard—the starting point for the calculation. The second color is the weathered panel. The Delta E number will provide the color change that is expected due to fade and loss of gloss after exterior exposure. The lower the number, the lower the amount of color change. The higher the number, the higher the amount of fading.
• Blistering:
Blistering represents a localized loss of adhesion and the lifting of the coating film from the underlying surface. This is caused by heat, moisture, or a combination of the two. This condition eventually leads to peeling and corrosion. Surface blistering can sometimes be caused by improper drying or curing of the coated material.
• Cracking/Flaking:
Hairline fractures occur in the coating that then splits and eventually peels away from the substrate to cause cracking and flaking. Improper application, spreading paint too thin, poor surface preparation, or improper paint selection for the environmental conditions can all cause cracking or flaking in a coating system.
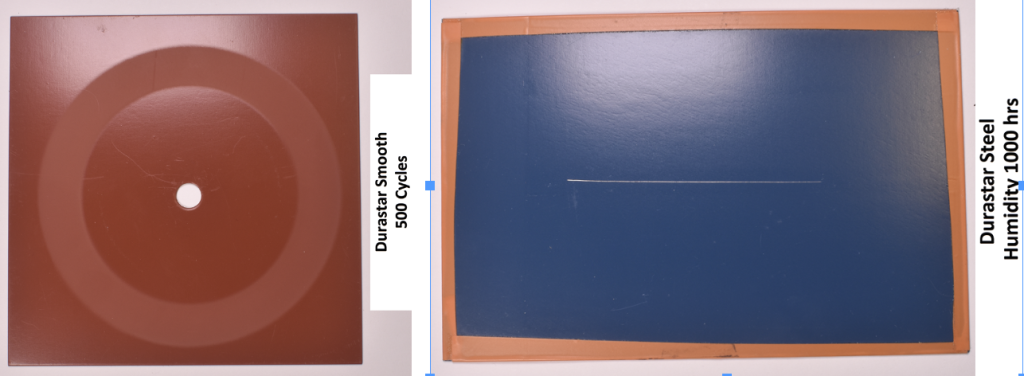
Regarding the overall process of testing coil coatings, Sarah Mueller, Coil Technical Manager for PPG Industrial Coatings, shared, “The continuous process of coil coating dictates the need for quick testing to confirm properly applied and cured paint film on the metal sheet. The tests run at the time of application include physical performance, appearance, and evaluation of proper cure with solvent resistance. Many of these standard test specifications were developed, documented, and standardized by ASTM International many years ago. The test methods used regularly include some wet paint property testing, which allows for standardization of properties needed for best wet paint application. Once the paint is coated and cured to a dried film onto the metal sheet, there are a variety of methods used to evaluate color, gloss, and physical properties like hardness, flexibility, adhesion, and solvent and chemical resistance. Additionally, there are also standardized methods for testing and evaluation when the metal sheets are exposed to accelerated weathering cabinets and outdoor weathering sites.”
Sherwin-Williams takes the same two approaches to weather testing: long-term natural exterior weather exposure and laboratory accelerated weathering. Each approach verifies performance, application, weathering, and appearance of sample panels. For natural exposure tests, panels are placed on inclined open racks oriented toward the sun. Waldroup shared, “Sherwin-Williams Coil Coatings’ A2LA testing facility in Ft. Myers, Florida, is home to 150,000 panels over 2.5 acres that are exposed at a 45-degree angle facing the harsh south Florida sun. This is an ideal location because the high UV exposure, humidity, temperature, and salt-spray conditions are so extreme. The panels are routinely monitored over time to ensure performance, including color and gloss retention. This test fence has been in place since 1968, so there is plenty of data to support their performance findings.”
He continued, “But new, innovative coatings couldn’t be introduced if we had to wait 53 years for complete testing. So, special environmental cabinets and instruments are used to speed up the weathering process and measure its effects under extreme conditions: heat, cold salt-spray, and humidity. The accelerated weathering cabinets duplicate the results of long-term outdoor environmental tests using chemicals and laboratory tools to see in just hours what years of exposure would do in the field. This testing is most useful in the development states of coatings to test various ingredients when formulating to see which ones will be the best choice for a particular coating.”
While these laboratory accelerated weathering cabinets are important for the development of coil coatings, they can’t compare to the results from natural weather exposure over the course of a multi-year test. No matter the testing process, “Sherwin-Williams focuses on what matters—a coating system that can last the test of time. The result is better coating formulas, better color retention, and longer life,” said Waldroup.
Developing New Products
Weeks, months, or even years of testing means it can take ages for a new product to be developed before it hits the market. Mueller said, “Development test cycles usually involve a scoping session and a test drill phase, which tests a variety of concepts to meet the key project objectives. The product is then developed to the needed criteria, tested, validated, and then launched with the applicators and end users.”
She added, “Changes to an existing product or technology can take between 3 and 12 months to develop, where new product technology can take many years to certify that the product will meet necessary specifications. New product technology timelines are longer, due to the need to gain data on the outdoor performance of a painted part. Project timelines can be narrowed down with the use of accelerated testing cabinets, which simulate weather conditions that the painted parts will be exposed to when installed outside, like saltwater exposure, ultraviolet light, and humidity conditions.”
AkzoNobel’s Brent Fletcher, Regional Segment Manager of Coil & Extrusion, explained their process of modifying an existing product or adding something new: “Some new products are modifications to existing technology that add a desired benefit (e.g. aesthetic or functional property). Under this case, the core chemistry isn’t changed and key understanding of performance is known. The development path under this scenario can be much quicker due to a certain level of understanding and confidence in the system. Short-term lab-simulated testing could be deemed appropriate to deliver this type of development.
“Technology completely new to the market containing unknown variables takes much longer to develop. This is especially true for premium products with strict performance and warranty needs. Testing for entirely new products includes a combination of short-term and long-term testing. Research often includes examining the entire system as a whole for performance. This includes substrate, pre-treatment, and all coating layers (primer, topcoat, backer). As mentioned above, time to deliver a new coil coating product to the market depends on the type of development, product specification, and warranty needs. The time frame to deliver new products could range from months to years for products with strict performance specifications and extended warranties.”
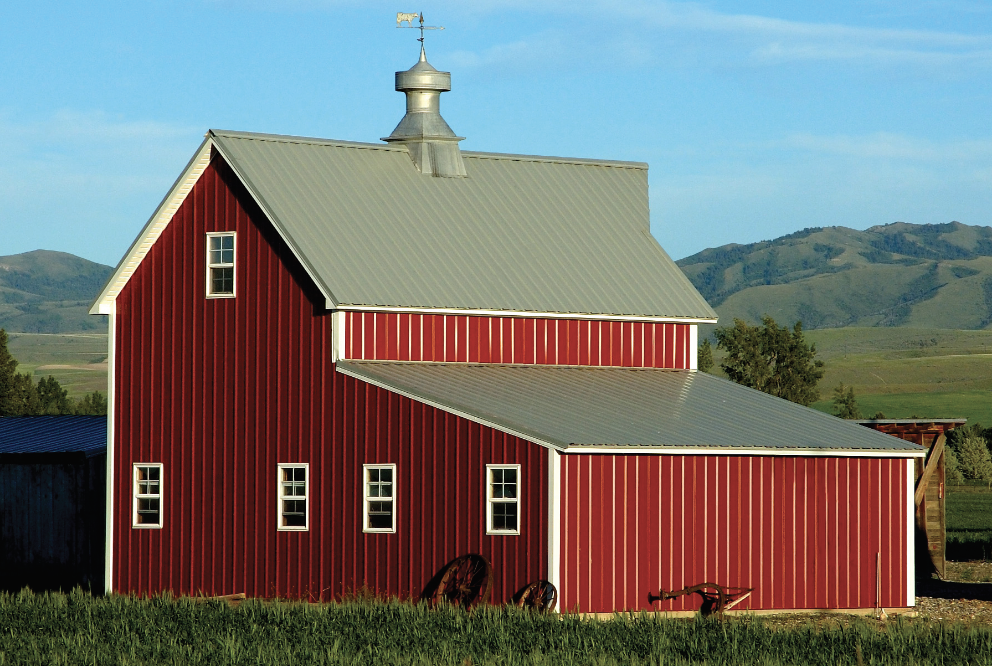
Sustainability of
Today’s Coatings
With the ever-increasing concerns about the environment and our affect on it, industries across the world are considering their impact during product development and testing. Mueller stated, “The coil coating process itself can be considered sustainable, as many coil coating lines have a thermal oxidizer unit, which cleans the gaseous burn off (volatilized solvents) of the coil bake process and reuses the clean heated air to power other plant operations.
“Many coil-painted materials are used in the building products market. Third-party organizations like LEED and the Living Building Challenge provide guidelines to designing sustainable buildings. Using these guidelines occasionally also allows for governmental benefits for building projects. One regularly used coating technology used for sustainable builds is ‘Cool’ coating technology. These coatings have also been commercially available for many years and are paint systems that are designed to reflect or refract sunlight away from the painted material, allowing for decreased energy consumption for the structure. These coatings can be used on roofing, side walls, and entryway structures,” she continued.
In conclusion, Mueller said, “Over the past few years, many end users and customers have transitioned to more sustainable materials. Certain heavy metals and additive chemicals have begun to be banned from use across the industry, which is cause for more innovation in the way we use available technology and materials and evaluate new raw materials being available in the market.” MR