By Derek Hodgin, PE, RBEC, CCCA, CXLT
I was recently given the opportunity to design a new roof for a resort property in Grand Cayman, British West Indies. My experience was pleasant, and the client is happy with the finished roof. However, getting through the project provided me with new lessons in roofing. I struggled at times, but I feel as though I have now graduated from Caribbean Roofing 101.
This story shares the highlights of my experience. I first flew to Grand Cayman in the fall of 1998 to perform my assessment of the existing roof and provide my recommendations for a new roof for the Christopher Columbus, a beautiful condominium resort at the north end of Seven Mile Beach.
The complex, built in 1978, consists of four buildings containing a total of 31 units. Each building has three roof areas which vary in height from one to three stories. The roof areas are constructed in Dutch hip configurations with a 3:12 pitch. The total roof area of the four buildings is about 26,000 sq. ft. The existing roof assembly consisted of a 5/8-inch plywood roof deck, roofing felt, and three-tab composition shingles. The assembly is supported by prefabricated metal-plate-connected wood trusses.
Some visible repairs had been made over the more than 20 years the assembly had been in place. These repairs consisted of roof shingles that had been removed and replaced and were observed on all four buildings, mostly near the eaves.
Additionally, approximately five years prior to my visit, an elastomeric coating was applied on top of the roof shingles. This coating protected the composition shingles from ultraviolet light and likely extended the life of the shingles themselves. However, it appeared that the elastomeric coating and the low slope of the roof was a bad combination. The paint was observed to bridge between overlying shingle tabs in some areas but not in others. Due to the low slope of the roof, the shingles were vulnerable to water penetration during high winds. Once the water penetrated the shingles, it could migrate laterally and become trapped under the elastomeric coating. Evidence of long-term water intrusion was noted in the discoloration of the white roof surface caused by corrosion of underlying roofing nails and soft areas in the plywood roof deck which were detected while walking on the roof.
I was given complete design freedom for the roof. Changing the roof framing was not an option, however. Therefore, I was able to quickly eliminate heavier roof coverings such as clay or concrete tiles which would exceed the capacity of the existing trusses. The client expressed a desire for a metal roof. However, the architecture of the buildings did not lend itself to standing seam panels, which are popular on many newer buildings on the island.
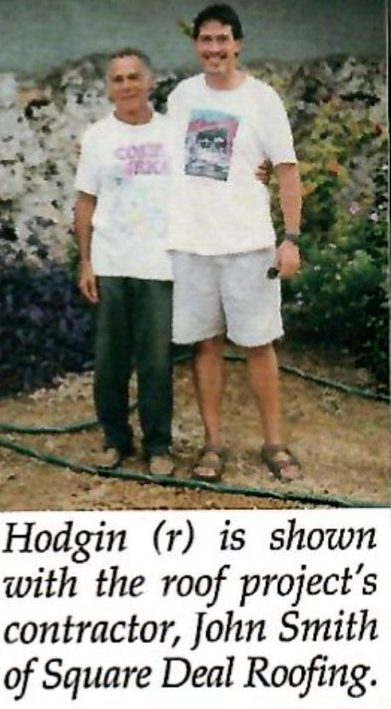
I had recently completed a roof project in Hilton Head, S.C., using Rustic aluminum shingles manufactured by Classic Products Inc. and was quite satisfied that this project would be well suited for a similar design. To make things even better, Classic Products has a certified roofing contractor on Grand Cayman, John Smith, owner of Square Deal Roofing. Smith is a Cayman native and the nicest guy you could meet. After discussing the project with Square Deal Roofing, we made a brief presentation to the client recommending the Rustic aluminum shingles. The client accepted the recommendation, and we were ready to begin the design process.
The New Roof
While I like the appearance of the Rustic Shingle and knew that I could adapt it to the design requirements, it presented a few shortcomings for the Christopher Columbus project. First, the profile includes a butt edge thickness of about 1 inch. Given the low slope of the project’s roofs, this could have been the only part of the roof that would be seen, particularly on the taller two- and three-story roof areas. This problem relates to the fact that it is difficult to observe the roofs from a distance. The property is bordered by a road and the beach on the east and west and by other resorts to the north and south. Second, the thickness of the profile creates a small void under the base of the shingle. Concern was expressed about possible damage from foot traffic. This would not be a concern on a steeper roof but would be on relatively low-slope roofs.
Classic Products informed me of a new Oxford Shingle that would address the concerns just described. The new shingle has a low profile, which would significantly improve the visual aspect. Additionally, the Oxford Shingle is fabricated from slightly heavier aluminum than the Rustic Shingles (0.024- vs. 0.019-in. thick). The thicker aluminum and the low profile would also reduce the chances of it bending or crushing when stepped on. Unfortunately, the Oxford Shingle was not scheduled to be in mass production until the following year. Therefore, specifying the Oxford Shingle would mean a higher material cost (about 20 percent more than the Rustic Shingle) and slower production. Even so, after reviewing the options, the client selected the Oxford Shingle and I proceeded with the roof design.
Design Basics
Engineering calculations determined that, for a design wind speed of 120 mph, the wind uplift pressure at the corners and perimeters would be approximately 135 psf. Given the relatively small size of the roof areas and their broken up geometry, this uplift requirement applied to a large portion of roof. A continuous 0.024-in. aluminum fastening cleat was specified in the 135 psf areas. The cleat attachment included a double row of stainless steel screws spaced at 12 inches on center. Individual fastening clips were specified in the field of the roof where the uplift pressure was calculated to be approximately half that of the corners and perimeter.
After the preliminary design was complete, a 10-ft. x 10-ft. section of the roof assembly was constructed by Classic Products and tested in a wind chamber to determine its uplift resistance. At the design uplift of 135 psf, the roof assembly was observed to be intact with no evidence of failure. The individual singles finally deflected and became disengaged at about 185 psf, representing a design factor of safety of about 1.4.
The roof deck preparation included removing and replacing any deteriorated plywood sheets (an unknown quantity at this point), fastening all the plywood roof deck to meet wind uplift requirements, and installing underlayment. The specified RoofGuard® underlayment is a hybrid woven product specifically designed for metal roofs. It’s manufactured by UPM-Kymmene Corp. W. Rosenlew in Finland and marketed in the United States by Drexel Metals Corp.
The First Day
The roofing project was to begin in the middle of August and be completed by the first week of October, 1999. The materials had already been transported from Classic Products in Ohio to Miami, Florida. A container ship was then enroute to Grand Cayman and scheduled to arrive before the project start date. My first lesson in shipping was that, while the shipment may arrive on schedule, getting your hands on it is an entirely different matter. On the day the project began, all of the materials remained locked in a container at the port in Georgetown.
While the project could proceed without the shingles for a week or so, the underlayment was needed immediately. In an effort to keep things moving, I instructed the contractor to proceed with the roof tear off and substitute a double layer of #30 felt which is available at the local contractor supply. With the necessary materials in hand, the contractor proceeded to tear off the first roof.
As the shingles were being scraped away, it was quickly apparent that the middle of a large plywood area was completely rotten. I expected the roof deck to be deteriorated (water stained, delaminated, minor decomposition) in some areas, but not rotten. The wood was dark brown to black in color and extremely soft. If the plywood was this bad in the field, I figured it would be even worse at the eaves as more of the roof was torn off. My fears were realized; the wood rot was widespread with no discernible pattern.
If the extent of rotten plywood was similar on the remaining roof areas, the plywood replacement allowance would be drastically exceeded. The contract provided for an allowance of 10 sheets of plywood replacement. In the end, 128 sheets were needed, costing the owners of the buildings considerably more than originally allowed.
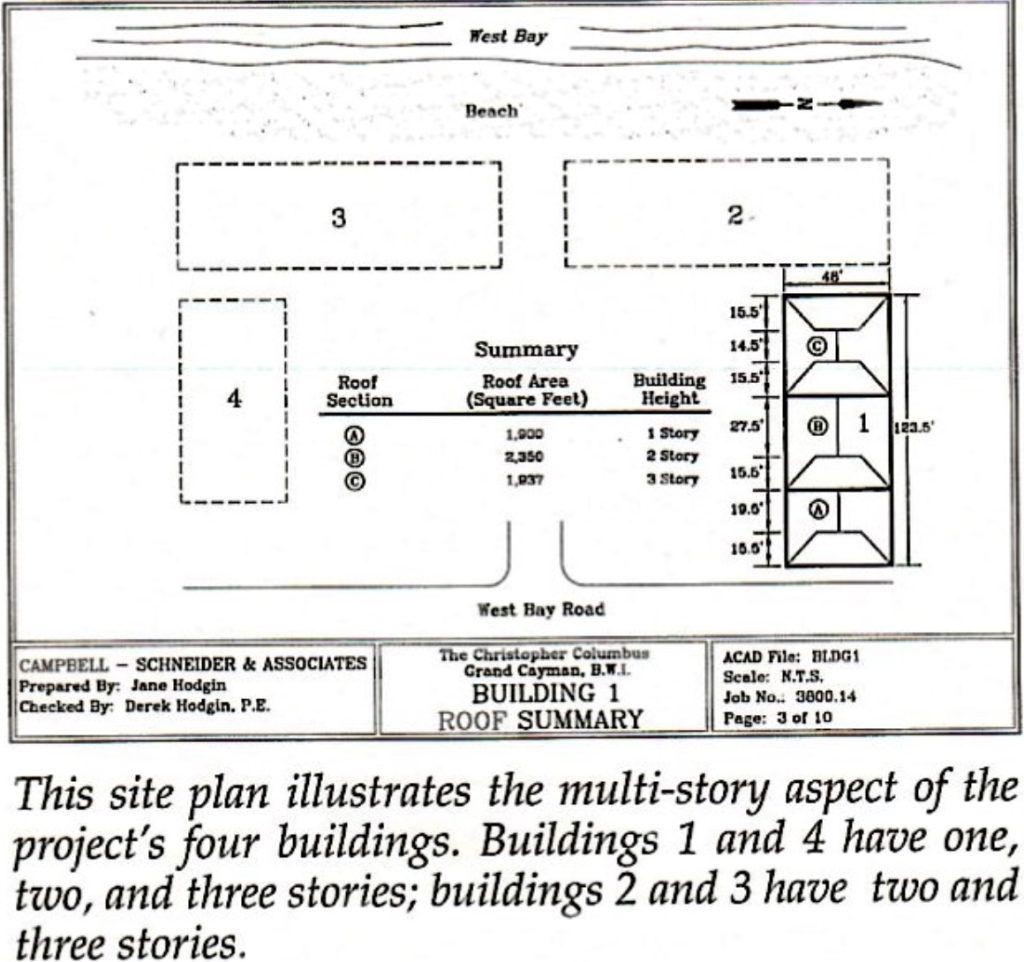
I am now convinced that my original assertion that the elastomeric coating was trapping water was correct. The extent of plywood damage and the significant corrosion of the roofing nails and flashing was the direct result of long- term exposure to this trapped moisture.
You Want It When?
The decision to use the Oxford shingle put the production at Classic Products into continuous overdrive. Because it was new, it was not yet being mass produced and each shingle had to be hand made for the project. This kept me continuously monitoring the materials at the site, the materials that were enroute, and the next possible shipping dates. Unfortunately, it seemed that there were always small gaps between the time we needed the materials and the time that they would finally arrive at the project site. This scenario resulted in a slow accumulation of delays which were stretching the project schedule.
Realizing that I would not even come close to meeting the specified project schedule, I informed the client of the available options: 1) complete two of the four buildings that year and come close to meeting our schedule, saving the other two buildings for the next year, or 2) forget about the schedule and proceed to complete all four buildings. After weighing the options the client, instructed me to proceed with all four buildings.
O.K., I had my new marching orders and I was ready to go full steam ahead toward completion of the project. I scheduled a return visit to Grand Cayman with renewed enthusiasm. It was a terrific 3 day visit. The weather cooperated and things were progressing nicely. In fact, by the time of my departure, the roof tear-off, plywood replacement, fastening and underlayment installation on the last two buildings was complete—and I had only recently been given the instructions to proceed with these buildings. Things were looking up.
Irene Pays a Visit
My hopes for a quick completion were dashed on my first day back in the United States. Hurricane experts were showing the development of a significant storm in the vicinity of Grand Cayman. The storm eventually grew into Hurricane Irene. I discussed storm preparations with the contractor. All of the construction materials were taken off of the roof and stowed in a secure place and the underlayment was battened down where possible. While I knew that there was not a lot that I could do from hundreds of miles away, I could not stop thinking about the potential consequences associated with this storm. I got the report on the following day: no damages to the roof or underlayment, although the ceilings of several units in the remaining two buildings were damaged by water. I was certainly disappointed, but tried to remain positive. It could have been much worse. However, the roof project seemed to be getting further from completion rather than closer.
Graduation Day
The storm damage was quickly repaired and the roof installation proceeded. In early February 2000, about four months later than originally anticipated, I got the call that I’d been waiting for.
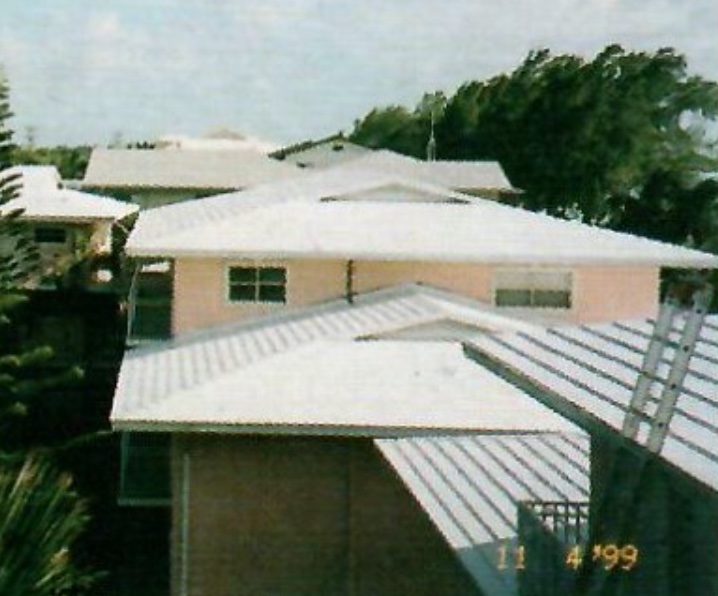
All of the roof work was complete and Square Deal Roofing was ready for the final inspection. I provided Square Deal with a copy of the very detailed punch list I planned to use in my final inspection. Square Deal diligently inspected every roof area in accordance with this list. My final inspection revealed only a few items to be addressed, none of them significant.
With all of the paperwork completed, final payments made, and the client satisfied with the new roof, I am happy to report that I finally graduated from Caribbean Roofing 101. I would like to take this opportunity to express my thanks and appreciation to Square Deal Roofing, Classic Products, the friendly staff at the Christopher Columbus, the understanding client, and my employer for signing me to this unforgettable project. MR
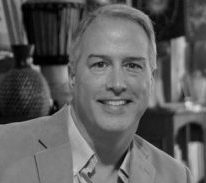
Derek A. Hodgin has 30 years of experience as an engineering consultant and is responsible for facility condition inspections, failure analysis, damage assessments, and forensic engineering investigations of all types of structures. His experience includes failure analysis of a wide variety of building enclosures and roof systems. He has investigated and testified regarding the performance of various building products including fire retardant treated (FRT) wood, exterior insulation and finish systems (EIFS), hardboard siding and trim. Derek has also designed, permitted and investigated failures of civil and coastal projects such as residential and commercial developments, marinas, docks, shoreline stabilization and retaining systems, basin and channel dredging. A large part of his projects have included analysis of deficient construction cases including roofs, exterior walls, windows, doors, structural framing, civil site work and building code review. He has investigated and testified regarding various types of personal injury cases including slip/trip and fall, railing failures, swing collapse and ladder accidents. Derek has performed engineering assessments of hurricane, tornado, hail, wind, ice and fire-related damages for a wide variety of commercial and residential structures.