When a metal roof begins to fail, most building owners assume they need a full new roofing assembly, whether or not the current one has reached its anticipated lifespan. Luckily, that is not always the case. Roof coatings have come a long way toward extending a roof’s life; retrofit systems can also save the hassle of removing the old, existing roof. Here, we dive into details on both sides.
“Team Recoat”
By Tim Simpson of Ames Research Laboratories
When choosing to recoat a metal roof, there are numerous factors to consider. First is selecting the proper coating system. It must bond well to the present metal roof, protect the roof from further deterioration, solve leak issues, and offer the desired finished appearance. The process begins with a roof survey to identify the condition of the existing roof, with the goal of addressing the following:
• What type of surface currently exists? Metal roofs can be made up of a variety of materials, including galvanized iron, baked-on enamels, fluoropolymer, or powder-coated metal, or could have been previously coated with aftermarket materials.
• The roof may need repairs to seams, fasteners, connections, penetrations, or surface-mounted item connections.
• The building owner may wish to reduce solar heat transmission into the building to lower climate control expenses.
Options for Various Roof Types
Due to the many variables in metal roofs and their factory-applied coatings, one roof recoating system may be a good fit for a certain type of roof while another may not. Existing coating technology, such as factory-applied fluoropolymer, was created from high-performance resins and fluoropolymer lubricants. These types of coatings are virtually self-cleaning, maintain a high gloss finish, and have excellent resistance against solar exposure. Recoating over this type of prefinished roof needs a careful approach, as cleaning, preparing the surface, applying a special bonding primer, and finish coating are imperative to create a finish that will adhere and perform well. This is due to the fluoropolymer additives in the existing coating that create a slick, hard-to-adhere-to surface. Install test areas of the proposed coating on the existing roof to confirm good bonding, etc.
When coating older galvanized metal roofing panels, the roof needs to be power-washed to remove any pollen, dirt, or loose oxidation of the zinc galvanizing. Newer galvanized metal panels also need to be checked for thin film oils, applied at the factory to prevent sticking of the panels during transport, and premature formation of white rust.
When coating existing metal roof panels that may have baked-on enamel, powder coating, or aftermarket paints, the surface also needs to be pressure-washed and tested for adhesion. The existing coatings may have oxidized over the years, leaving a visible film that can rub off. A rule of thumb is if oxidized residue rubs off on your finger, the surface needs to be cleaned thoroughly—possibly with the assistance of a detergent.
If the metal roof has seam, fastener, flashing, or penetration issues, the manufacturer’s recommendations for completing detail repair work need to be adhered to. On a deteriorated roof, this detail work can get quite extensive, taking as long to complete as the actual coating’s application (or longer).
Coating Application
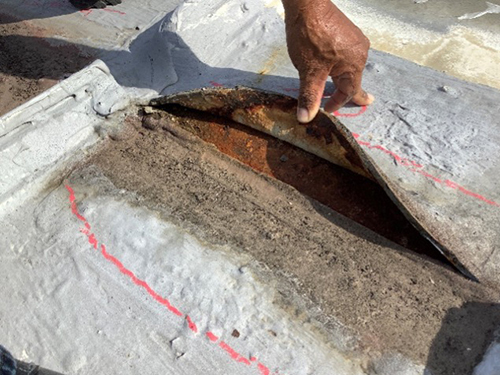
Properly applying the coatings is the next step, while keeping these considerations in mind:
• Have you applied a field sample or panel so the owner can approve the product choice? They will want to see the sheen, color, texture, and overall uniformity of the surface.
• If roller-applying, the nap of the roller can change the reflective values and apparent sheen of the finished product. If too much texture exists to apply by roller, then spraying may be the best option. However, spraying triggers an additional set of concerns, such as overspray, which may require extensive masking.
• Weather is always a consideration when coatings are being applied to metal roofs. The coating manufacturer’s recommendations need to be followed closely during both the application and cure time. Too-cool weather could slow or prevent proper curing, and too-hot weather could create sheen and texture issues. Extremely hot weather can prematurely cause coatings to surface skin over before the material has properly evaporated its solvents or water. This can create entrapment of uncured material under the surface—considered a coatings failure.
The benefits of recoating an existing metal roof in lieu of installing a brand-new metal roof are many:
• Recoating of existing metal roofs is less expensive than replacement.
• Applying solar reflective coatings to an existing roof can give better energy performance than simply replacing one metal roof with another.
• There is less disruption to many facilities when a roof is recoated, as material staging areas are smaller and the overall work footprint is reduced.
• Site debris and pollutants are drastically reduced.
• Less overall energy is consumed in recoating than in a full tear off and replacement.
• Exposing the roof to leaking while the roof is removed is not a consideration when over-coating the existing roof. In some areas subject to frequent precipitation, this can be a big concern.
When to Consider a Full Replacement
Although some repairs may be needed with roof recoating projects, there is a point where a full replacement should be considered, such as:
• The metal has deteriorated to the point of being structurally unsound.
• The existing roof has been deemed “uncoatable” by coating manufacturers.
• The roof has been damaged by hail or is otherwise no longer aesthetically viable if visible to the public.
• The combined cost of repairing and recoating the roof is greater than the cost to replace the roof.
When considering warranty requirements for owners, available warranties can vary depending on the number of coats applied, if the coating system required detail work that has been completed, and if certain quality control measures have been followed. Manufacturers’ warranties are frequently for material performance, and the contractor applying the materials is responsible for issuing an installation and service warranty.
Metal roofing contractors often deal with many repeat customers and rely on making well-informed recommendations. Installing a metal roof may result in the same customer calling years later for advice on replacing, repairing, or recoating the roof. Common sense would dictate that the best value for your client is also the best for you in the long run, as satisfied customers tend to lead to referrals. Recoating of aged metal roofs can be a valuable tool in your tool pouch for creating additional sales.
“Team Reroof”
By Dale Nelson, President of Roof Hugger, LLC
Every year, building owners and contractors coat many millions of square feet of existing metal roofs with several different products. Why do they do this and what do you gain by coating?
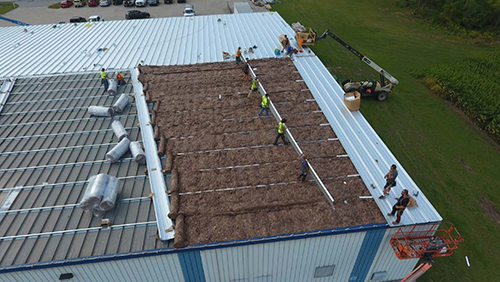
The reasons are varied, but basically can be boiled down to a few major problems:
• Roof leaks (the most common)
• Desire to improve the thermal efficiency of the existing roof
• Extending the remaining life of the existing metal panels to put off replacing the roof
So why recoat an existing metal roof as opposed to installing a new metal roof?
• The first answer is easy: Coating an old metal roof is cheaper than installing a new metal roof.
• The reflectivity of the roof is increased.
• The surface corrosion is slowed.
• In the case of liquid-applied roofing, you have the above benefits plus the roof leaks have been stopped.
Catches to Coating
That all sounds great, but is there a catch? Yes, there are several:
• Before you coat anything, remember many metal roofs have 25-year (or more) finish warranties. Coat it, and you will void any warranty that may exist.
• A simple roof coating is not intended to stop roof leaks—it may for a while, but it will be short-lived.
• The cost is between 25% and 70% of a new metal roof.
• The reflectivity achieved when the coating is new is typically reduced by 60% by the end of the first year without regular maintenance.
• All coatings must be applied to a clean, dry, and oil-free surface. Badly rusted metal roofs are very difficult to properly prepare. Prep and good application are critical to getting a good bond. Metal roofs have lots of edges and irregular shapes to cover: fasteners, penetrations, end-laps, side laps, ridge caps, rake edges, etc. Blisters, pinholes, fish eyes, craters, and other imperfections are common in coating applications.
• Metal roofs are always moving. A typical 26-gauge steel roof will expand about 1″ per 100′ of panel run. When the roof heats in the sun or a cloud passes over or it gets rained on, the metal moves. This thermal cycling occurs all day, every day, so the coating must stretch and contract also.
• Constant movement and UV exposure leads to the coating breaking down and cracking (some very quickly).
• Imperfections from application problems and thermal/UV cracking will trap moisture between the coating and the metal roof. This trapped moisture will actually accelerate corrosion of the metal and reduce the remaining life of the panels.
Why to Go the New Roof Route
So why would a new metal roof be better than coating the old one? A few reasons to consider:
• A new metal roof can often be installed over the existing metal roof, minimizing disruptions to ongoing operations.
• It will increase the thermal efficiency of the roof. Retrofitting over the top of the existing roof creates a cavity that can be insulated and/or ventilated to increase the energy efficiency of the building.
• The new roof will be compliant with current building codes. Many old roofs were designed to withstand 80 to 110 mph winds. The new codes starts at 110 mph and go up to 175 mph and beyond.
• The new roof will meet the current snow load requirements (that have also increased in many parts of the country).
• A new zinc-aluminum (Galvalume or equal) coated metal roof has a 60-year service life. Twenty-five years and beyond weathertightness warranties are available.
• Old screw-down roofs can be upgraded to new standing seam roofs, which are also the ideal platform to add future photovoltaic systems.
Why spend 25% to 70% of the cost of a proper, fully code-compliant metal roof for a short-term solution that only moves the repair back a couple years? You can put a patch on an old, bald tire and it may last for a little while longer, but you still have an old, bald tire. Coating will not make an old metal roof a new metal roof—only a new metal roof will do that.