Warranties are an essential part of selecting the right metal roofing for your customer’s home. There are many points of consideration but three of critical importance are the ones for the paint, metal substrate and the installation. The best product in the world has no value if problems show up and there is no one to repair it. There are two important areas of warranty responsibility—manufacturer and installer.
To start down the path that will maximize your customer’s experience, make sure they receive a physical copy of all relevant warranties and invite them to read them. Warranties and how issues are corrected when claims emerge are not all equal in scope. Costly disputes can be avoided with a well-documented warranty. Understanding what the manufacturer covers will help you understand what issues may be considered uncovered and looked at by customers as installation related.
Are there clauses that require general continual inspections at certain time intervals to maintain the warranty? If a repair is performed are there recertification/inspection timeline constraints? Make sure the expectations are put in writing.
Failure to perform those inspection/recertification tasks may void a customer’s warranty. Does the installation warranty you offer transfer with the sale of the home? If so, does it transfer with or without a fee? What is the time window for the transfer to take place?
What about pro-rated warranties where the coverage of remedies decreases as the acceptable degradation increases? For example, what happens if there is damage over a period of time and a segment needs to be replaced? Is there manufacturer coverage to make sure the look will match the rest of the aged roof that is intact? How is the degradation amount determined and by whom?
Metal substrates also have warranty considerations. It is very important as an installer to know the manufacturer and make sure they have been in business long enough to support the warranty they are offering your customer. A “Lifetime” warranty from a company that folds in a couple years and recreates itself will not help with warranty issues.
Is there a clause that covers rust or perforations of the substrate? If so, how long will there be coverage? Galvanized steel often has its corrosion protection evaluated in relation to the amount of zinc coating on it. Galvalume can have different thicknesses of its coating alloy of aluminum and zinc.
Coatings also have special warranty considerations. It is important to know the thickness of the paint system being used on your base metal substrate. They are not all the same. Where and when was the paint applied? What degrees of chalk, fade and film integrity are covered for what length of time? The standard for fade is usually measured by ASTM methods. The units of fade are referred to as Delta E or NBS. A Delta E change that can be seen by the naked eye is a 1-2. Generally, fluoropolymer finishes cover fade for a 30-year period with a maximum change of 5 Delta E units. If the paint system is not warranted, it is very possible your customer may encounter greater fade levels.
Chalking forms on the paint’s surface due to the decomposition of the resin. Lesser quality finishes are more likely to produce higher amounts of chalk. It is important to consider the environmental stresses that will accelerate this decomposition like heat, moisture, and exposure to UV rays to make sure you are using the best product for your customer.
What happens if a product is later found to be defective or is damaged and needs repair? Understand if one of the warranties covers the corrective installation costs. It may or may not, and that is important for your customer to know. If rooftop solar panels are installed and need to be removed to do a substrate repair, who takes the solar off to fix the area covered under the warranty repair? Who covers the cost?
Do you have the documented history of warranty fulfillment to give your customer confidence in your installation warranty? Are there examples of when something has gone wrong with an installation and you have made it right? Keep those examples in your back pocket in case you are asked, because it demonstrates your commitment to the type of customer service that results in customer satisfaction.
There are many things to look at when comparing warranties for metal roofing components. Those who respect and responsibly handle their customers will be happy to explain all the protective benefits they offer their clients, both short term and long term for the substantive and aesthetic components of the products they are seeking. Metal roofs are truly a desired investment for those seeking the low maintenance, long-lasting solutions for their homes. It is worth the time to understand exactly what is backing the investment of time and money your customers are putting into their metal roof. MR
Tracy Schubert is a book editor at Shield Wall Media, LLC. Schubert has edited more than a dozen books over the course of her career including the 2022 release, Pro Tips On Your Metal Roof.
By Tracy Schubert
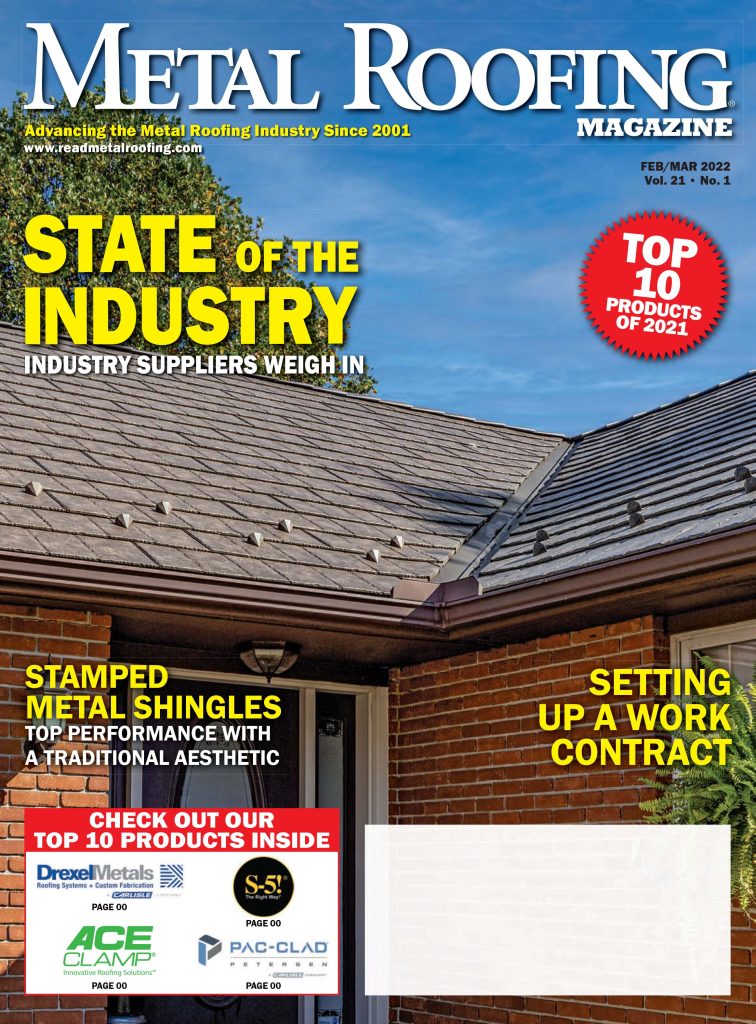
Sign Up For A Free Subscription
Anyone who is involved in the construction trade is welcome to sign up for a free print or digital subscription to Metal Roofing Magazine, which has been advancing the metal roofing industry since 2001. This go-to resource for metal roofing professionals is published 7 times per year.