By Jessica Franchuk
In 2010, 123.3 million people lived in U.S. coastal counties according to a report by the National Oceanic and Atmospheric Administration’s (NOAA) Office for Coastal Management. That’s a lot of people, who require a lot of residential structures, which need a lot of roofs. Faced with salt spray exposure and hurricane-force wind and rain, more and more seaside homeowners are choosing metal roofing due to its hardiness, longevity, and proven track record along the coast.
The NOAA also states that annually, coastal counties produce more than $8.6 trillion in goods and services—the businesses producing this money are housed in commercial, industrial, agricultural, or residential buildings, which also need roofs. With 22 states boasting saltwater coastline, the U.S. roofing market requires solutions that can stand up to this often-harsh environment. Here are areas to consider when bidding a metal roofing job by the sea.
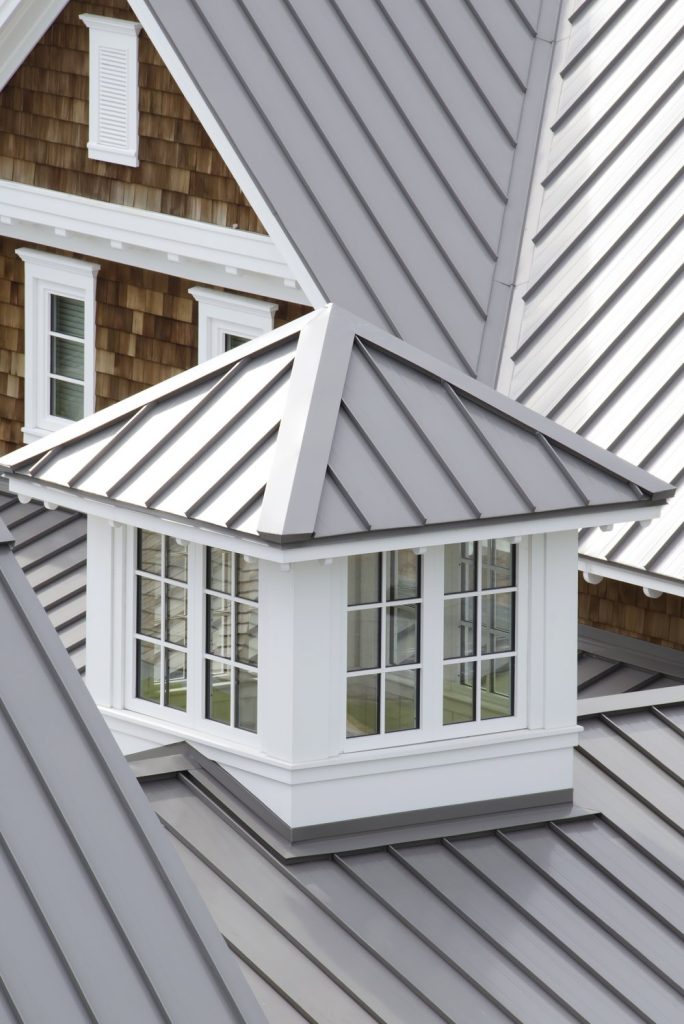
Metal Types
Travis Lord, Product Manager for The Garland Company, said, “When on the coast, typically the go-to will be .040″ or .050″ aluminum. Stainless steel and zinc are also great options, but tend to be more expensive. Aluminum is more cost-effective than stainless steel and zinc and still does a superb job at handling salt-spray environments.” He recommends avoiding galvanized steel as it can rapidly corrode in this environment.
Drexel Metals’ Director of Sales, Ken McLauchlan, added that while aluminum is more corrosion-resistant than steel (and is lighter), it is also softer. The entire roof system will be less of a load on the structure, but won’t stand up to the punishment of a severe hailstorm as well as steel.
Natural metals are often said to perform best, as shared by Robin Anderson, Technical Manager for Boral Roofing, who noted about each:
Copper: Though highly corrosion-resistant, copper does not have the strength of steel. Warranties and wind performance may be lower than other materials. Patina can stain areas of runoff. Has a high cost and is heavier than other metals.
Aluminum: Though highly corrosion-resistant, also does not have the strength of steel. Warranty and performance to winds may be lower than other materials. Patina of aluminum oxide will dull the bare color.
Zinc: Though highly corrosion-resistant, does not have the strength of steel. Warranty and performance to winds may be lower. Patina darkens the coloring and the cost is high.
Anderson also added that alloys can bring added benefits:
Stainless Steel: Strong; has some corrosion to fasteners of carbon steel.
Galvanized Steel: Strong. Shorter resistance to salt corrosion. Has setback requirements from the water.
Zinc-Alum Coated Steel (commonly known as Galvalume®): Strong. Has a higher resistance to corrosion than galvanized.
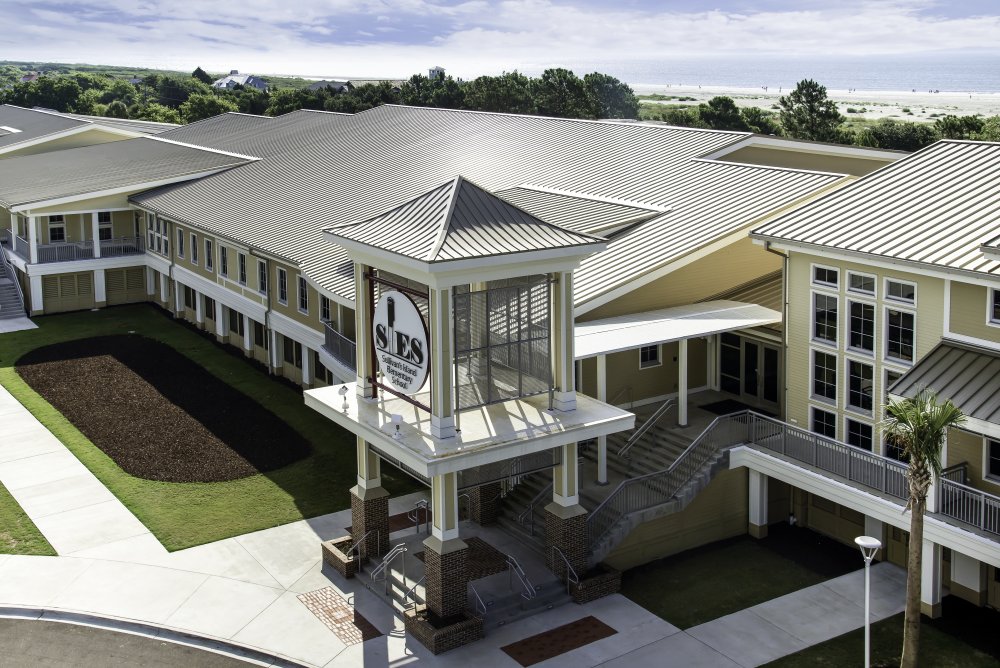
Coating Options
Once a metal type is chosen, next up on the list of considerations is the coating/finish. According to Lord, “It is important to utilize a coated metal when on the coast. Bare metal is much more prone to oxidation, [with] nothing stopping the salt spray from interacting with it. A Polyvinylidene Difluoride (PVDF) coating is recommended to help keep the substrate metal free from oxidation. A two-coat coil-applied PVDF system will help resist the harsh coastal environment.” Another option is stone-coated steel, which can provide prolonged resistance.
Many coil coating companies make systems specifically designed to resist the issues commonly plaguing coastal roofs. Sherwin-Williams Coil Coatings offers Flurothane® Coastal, “a two-coat system that uses an innovative thick-film primer to thrive in the most severe coastal environments.” This premium fluoropolymer 70% PVDF system was created to deliver long-lasting protection for industrial, commercial, or architectural projects within 1,500′ of the coastline. The system has been field-proven and provides a high-performance finish, as well as the following unique benefits: outstanding resistance to UV rays, exceptional color retention, and resistance to chalking from salt spray and harsh coastal environments. Flurothane® Coastal coatings can be applied to a variety of substrates, including Hot-Dip Galvanized (HDG), Galvalume®, and aluminum.
Clamps, Clips, and Fasteners
After the metal type and coating are determined for the specific job, you must consider how to keep the roof on the building. Many coastal areas are subject to hurricanes, which can bring sustained winds from 74 mph to 157+ mph. S-5!® shared when considering metal roof types in coastal areas, an important factor is extreme wind forces that will try to tear any roof from its mountings. Standing seam metal has a distinctive advantage over other membrane and asphaltic roof types because it serves as a “structural” covering, meaning it can be engineered to withstand almost any forces imposed by wind. Increasing the frequency of attachment, increasing the gauge thickness of the metal, decreasing the panel width, and using S-5!® external “WindClamps™”, or any combination of the above, will generally increase the durability of the roof in a windstorm. These remedies are not guesswork, but a matter of science, engineering, and testing. The S-5!® solution alone can increase wind resistance up to three-fold.
Rob Haddock, CEO and Founder of S-5! Metal Roof Innovations, explained: “Wind speeds are converted to negative pressure exerted on the roof; this pressure is often called ‘uplift.’ The conversion is a complex mathematical and geometric one governed by engineering standards (ASCE-7) and/or local code authorities. The transfer of the computed forces from the roof covering into the building’s structure involves a number of factors and components, including the strength of the seam itself, the strength of the clip’s attachment to the seam, the strength of the clip itself, and finally the clip’s attachment to the roof deck or structure (the clip screws). These components comprise a ‘load chain,’ which is only as strong as its weakest link. Because of the complexity of this load chain, most often its strength is determined by full-scale assembly testing.”
Haddock suggested consulting with the roof system provider to ensure the assembly proposed is proven to meet the wind speeds specific to the project’s location and set forth by the code authority having jurisdiction (AHJ).

Regarding fasteners, Direct Metals Inc. President Andrew Mullen said, “A fastener is the common way the metal roofing panels are secured to a roofing system substrate. The selection and installation of roofing system fasteners and screws have a direct effect on the performance and service life of these systems. Understanding how a fastener is chosen and performs within the roofing system is an important component of being a professional installer. It would be logical to assume that the roofing fasteners that come in a metal roofing package are expected to give corrosion-free performance for the life of the panel they are securing; that is not necessarily true. Many factors affect the corrosion resistance and holding power of a fastener (including selection of the proper fastener installation tool), but one of the main determining factors is proximity to highly corrosive coastal areas subject to yearly wind events.”
Mullen continued, “There are two main types of metal roofing systems: exposed fastener and concealed fastener. There are four typical substrates that these systems will be installed into. The choice of the correct fastener will be determined by a combination of factors, including the roofing system type, substrate, panel alloy, and expected life cycle.”
Lord added that stainless steel fasteners should be used in coastal regions, even for concealed fastener systems. The stainless will work well with aluminum roof panel systems. The use of stainless steel fasteners is even more critical for through-fastened systems or exposed fasteners in general. If the fasteners that are designed to hold the roof in place rust and fail, it could potentially lead to a roof blow off. A less extreme scenario from oxidized fasteners could be simply that the roof leaks because the fasteners rust so much that they create voids in the connection, losing their watertight seal.
Atlas Building Products agreed that they would not recommend an exposed carbon steel fastener in a coastal/tidewater environment—this will lead to deterioration of the fastener and red rust at a more rapid rate. If the fastener is exposed, they suggested a zinc die-cast head fastener as the superior choice to prevent against red rust in coastal/tidewater environments. Ultimately, Atlas felt the best option is to install standing-seam panels with stainless steel clips, along with concealed stainless steel fasteners.
According to Mullen, coastal areas and the proximity of structures to areas of saltwater fallout substantially increase the corrosion possibilities of roofing systems and their fasteners. Installers of exposed fastener panels should be using premium corrosion-resistant fasteners and not just an everyday galvanized “economy” fastener. “There has been a great advancement over the past 20 years in longer-lasting, premium exposed fasteners designed to provide years of corrosion-free performance, such as stainless steel cap head fasteners and zinc alloy capped fasteners. In coastal installations as near as 3,000′ from the shore, the FEMA recommendation is full 300 series stainless steel in both exposed and concealed building fasteners,” he explained.
Regarding fastener and panel compatibility, Mullen continued, “The popularity of corrosion-resistant alloys, such as aluminum panel installations, has grown in coastal areas. It is important to understand the differences between metal alloys and how bare dissimilar metals in certain environmental conditions can have serious reactions that promote premature corrosion and degradation.
“When working with aluminum panels, it is particularly important to understand the exposure to agitating factors such as proximity to saltwater fallout, moisture, and air movement. The installation of exposed fastener aluminum panels should be done with an all-aluminum fastener to avoid dissimilar metal reactions. If aluminum fasteners cannot be found for the application, a best practice approach of predrilling a pilot hole slightly larger than the fastener diameter and then sealing all edges of the hole with a barrier coating or sealant prior to fastener installation can lessen the chances of a reaction.”
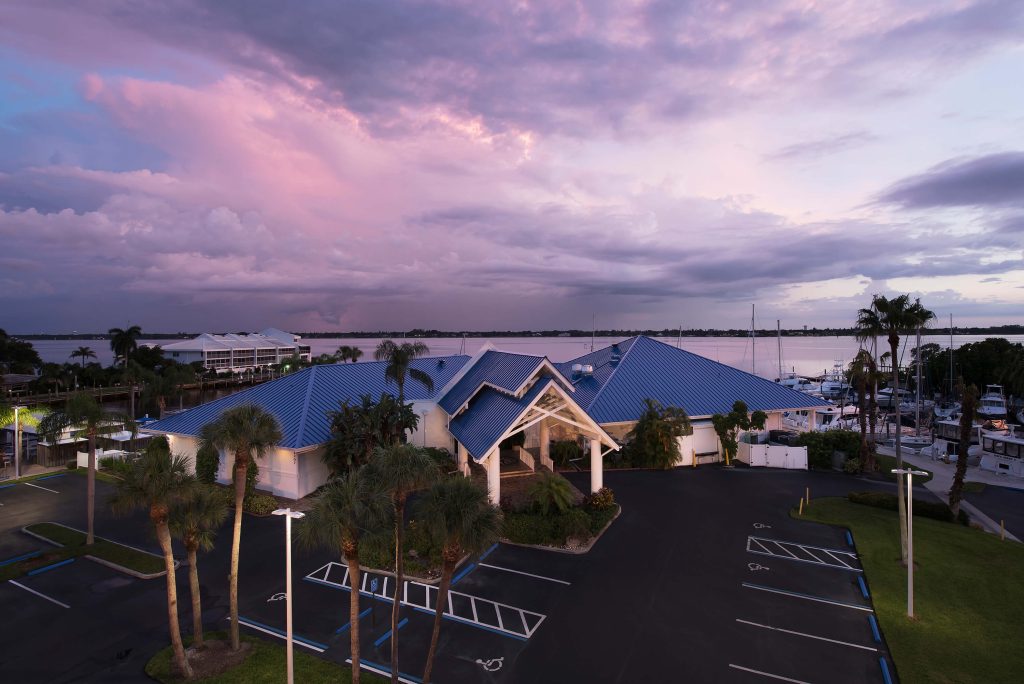
Underlayments
Lord said that underlayments are typically recommended in metal roofing, and a high-temp, self-stick, self-sealing underlayment should be used whenever possible. This acts as just another layer to what should be a “belts and suspenders” style of waterproofing. Anderson added that the underlayment chosen should be tested for high winds and pass ASTM standards for D-1970 (nail seal-ability).
“It’s crucial to specify a metal roofing underlayment material that is designed to protect the structure from extreme weather elements specific to the region where the roof is being installed. This can include water seepage caused by ice dams and wind-driven rains, as well as extremely hot and/or cold weather,” stated McLauchlan.
Codes and Testing
Code compliance and product longevity are always on the list of things contractors need to consider when choosing products for each job. Mullen said, “Forces that exact change can be small or large, such as the force of hurricane winds—the same winds that necessitate building codes and standards in Florida. Building codes promote the use of higher quality materials expected to increase the structural rigidity and extend the life of the building. These standards are quickly being specified, adopted, or mandated by many coastal cities, counties, and insurance bodies to encourage responsible building practices.
“Examples of code requirements and recommendations include the 2014, 2017, and upcoming 2020 code version of the Florida Building Code, which requires corrosion-resistant fasteners for roof assemblies. FEMA has written recommendations that coastal construction and high-wind areas only use stainless steel fasteners for roofing within 3,000′ of a body of saltwater. The Miami-Dade County Code compliance office has also implemented a fastener listing program that outlines additional corrosion-resistance and shear strength standards required for metal roofing fasteners, both concealed and exposed. If you are building in coastal or building code regulated zones, it is suggested that you determine if the fasteners in your system have certification listing numbers or meet building code guidelines and offer the corrosion resistance warranted by corrosive coastal environments.”
Lord added that certain areas of the country (Miami-Dade, Florida, Texas, etc.) have special requirements to be met in order for metal roof systems to be installed. Most of these requirements are derived from catastrophic hurricane events, such as Hurricane Andrew in 1992. These requirements are essentially roofs that are designed and attached to withstand extremely high wind uplift forces. Typically, a manufacturer proves this design through testing their assemblies and providing the results to either an approvals agency or the authority having jurisdiction in that region or area. “A customer should expect a manufacturer to be able to provide testing and approvals information to show that their roof system can handle the harsh wind uplift forces that that roof will endure,” he said.
Sherwin-Williams Coil Coatings conducts their own weather testing, which has become critical in preventing product failures. Innovation matters to the company, which continues to improve the performance and durability of their coating systems through research and development: “A well-planned weathering test program could identify coating failure risks in advance. With this, new formulations are created and need to be tested to failure.” From their Weatherability Matters literature, the potential failures they test for include:
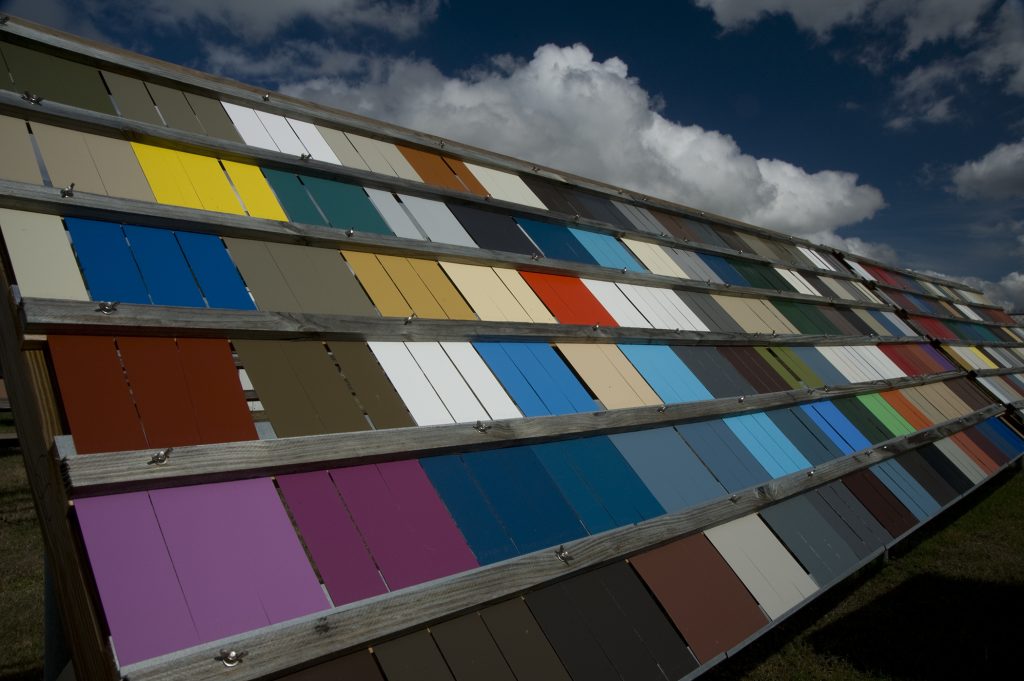
Gloss Retention: Gloss refers to a coating’s ability to reflect light without it scattering. Direct UV exposure can degrade the luster of the topcoat. While all types of coatings will lose some degree of gloss over time, lower quality paints will generally lose gloss much earlier than superior coatings.
Chalking: Chalking is caused by degradation of the resin system at the surface of the finish due to exposure to UV rays. As the resin system breaks down, resin particles take on a white appearance and embedded pigment particles lose their adhesion to the film. Chalking is tested by transferring the chalk to fabric or adhesive tape, then comparing it to a photographic reference standard (ASTM D4214). The range is from 10 to 1, with 10 showing the least amount of chalking and 1 showing the presence of extreme chalking.
Fading/Delta E: Delta E (dE) is a single number that represents the distance between two colors. One color is always the standard—the starting point for the calculation. The second color is the weathered panel. The Delta E number will provide the color change that is expected due to fade and loss of gloss after exterior exposure. The lower the number, the lower the amount of color change. The higher the number, the higher the amount of fading.
Blistering: Blistering represents a localized loss of adhesion and the lifting of the coating film from the underlying surface. This is caused by heat, moisture, or a combination of the two. This condition eventually leads to peeling and corrosion. Surface blistering can sometimes be caused by improper drying or curing of the coated material.
Cracking/Flaking: Hairline fractures occur in the coating that then splits and eventually peels away from the substrate to cause cracking and flaking. Improper application, spreading paint too thin, poor surface preparation, or improper paint selection for the environmental conditions can all cause cracking or flaking in a coating system.
The company takes two approaches to weather testing: long-term natural exterior weather exposure and laboratory accelerated weathering. Each approach verifies performance, application, weathering, and appearance of sample panels. For natural exposure tests, panels are placed on inclined open racks orientated at the sun, usually at a 45-degree angle in a southerly direction (this angle ensures full UV exposure). For accelerated testing, special environmental cabinets and instruments are used to speed up the weathering process and measure its effects under extreme conditions.
The centerpiece of Sherwin-Williams Coil Coatings’ exposure sites is a 6¼-acre facility in Fort Myers, Florida. Based on its subtropical location, this weathering site provides perfect conditions for natural exposure testing. “The site has 100,000 panels on exposure and a laboratory staffed with experts to review results and complete accelerated weather tests,” the company shared.
Warranties
Lord commented that a good manufacturer will offer not only a long-term waterproofing warranty, but also a finish warranty for the paint finish on the roof. A contractor should also offer a workmanship warranty for their installation. These should be in place so the manufacturer, contractor, and most importantly, the customer all understand responsibilities and know who to turn to if there were to ever be any issues down the road. MR
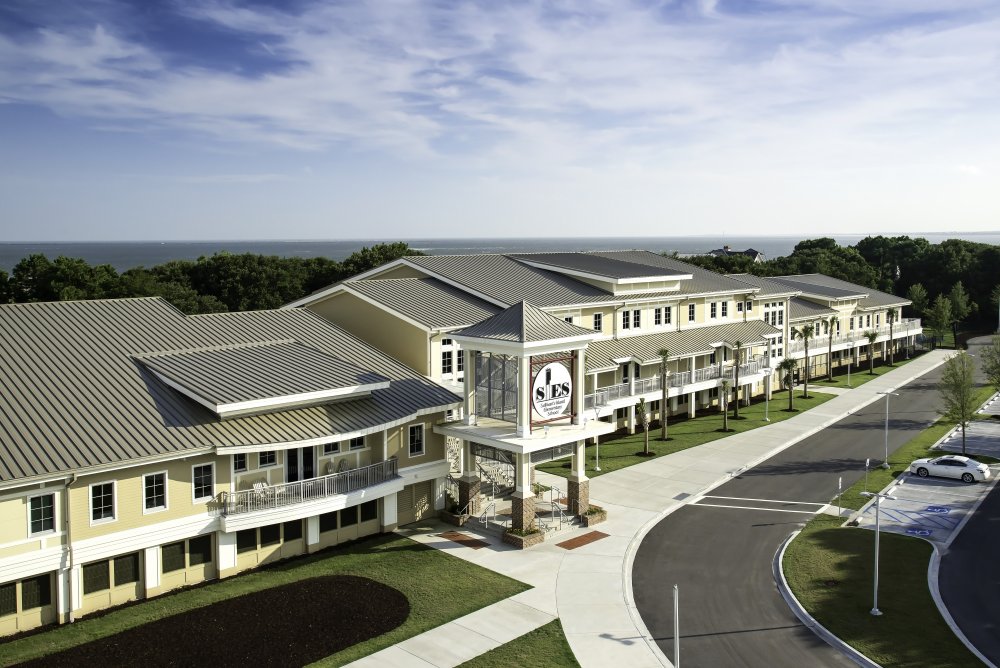