By The Metal Construction Association (MCA)
The Metal Construction Association [www.metalconstruction.org] brings together the metal construction industry for the purpose of expanding the use of all metals used in construction. MCA promotes the benefits of metal in construction through technical guidance, product certification, educational and awareness programs, and many other initiatives. This technical bulletin by the MCA was originally published in 2018 and is reprinted here with permission.
Metal roofing and siding panels are made with the highest recycled content from the most recyclable materials on earth, making them a great choice not only for today, but for future generations to use. Your old steel car, soup can or washing machine may become part of your new roof or siding material! The federal government and most states are mandating energy-saving requirements for buildings or giving tax breaks for energy-efficient and energy-saving construction products. Because recycling decreases the amount of energy required to produce metal products, recycled content is also being recognized and rewarded, making recycling an economic as well as an environmental benefit.
California, New York, and Pennsylvania are leading the way in energy-saving initiatives, using the “Leadership in Energy and Environmental Design” (LEED)® rating system to certify “green” buildings under the system created and promulgated by the U.S. Green Building Council (USGBC).
Energy savings also come from many other efforts including design considerations such as landscaping that saves water or highly reflective metal roof finishes that reduce air conditioning load to save energy.
Steel Recycling
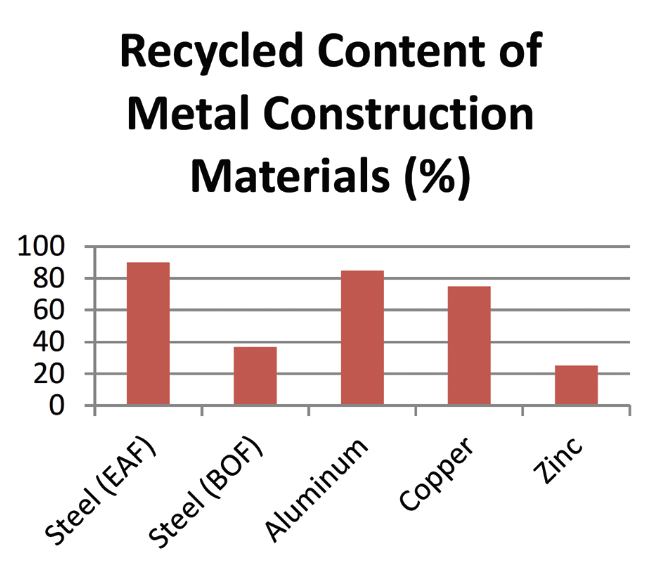
Steel is the world’s most recycled material. Every year between 60 and 80 million tons of steel are recycled in the U.S.
Two different processes, the basic oxygen furnace (BOF) and the electric arc furnace (EAF), are used to produce steel. Both processes utilize available recycled scrap steel to produce new steel.
Steel construction products contain significant levels of recycled content. Additionally, many steel products recovered from demolition or retrofit projects are suitable for reuse. The LEEDv4 Reference Guide (page 535) allows a default value of 25% post-consumer recycled content for any steel product. However, some steel products (e.g. structural sections and reinforcing bar) may have recycled content levels as high as 100%. These higher values may be used in the LEED credit calculations if company-specific recycled content information is available from the steel product supplier. As described in the LEEDv4 Reference Guide (page 536), “industry-wide or national average recycled content values may not be used in calculations to support achievement of this credit.”
Care should be taken when making environmental comparisons between steel made by the BOF and EAF process. Both are part of a complementary steel-making system.1
Aluminum Recycling
Aluminum is also recycled extensively from both pre-consumer and post-consumer sources and provides the most valuable component for most municipal recycling efforts. A survey in mid-2008 indicated that the recycled content of domestically produced, flat-rolled products for the building and construction market was approximately 85%. The survey of producers indicated that on average about 60% of the total product content is from post-consumer sources. In addition, at the end of a long, useful life, aluminum roofing and siding panels can be repeatedly recycled back into similar products
Producing aluminum from recycled material requires only 5% of the energy required to produce aluminum from bauxite ore and every ton of recycled aluminum saves four tons of bauxite. Additionally, using recycled aluminum instead of new materials reduces air pollution generation such as CO2, SOx, and NOx by 95% and water pollution by 97%.2
Copper Recycling
Copper also is routinely recycled with the highest scrap value of any building metal. Copper’s high cost makes it a favored product for collection and sale to nonferrous-scrap recycling companies. The scrap is melted down and reformed into a new, appropriate product. This re-melting takes only about 15% of the total energy consumed in mining, milling, smelting, and refining copper from ore.
The average recycled content of all copper products is 44.6%. Copper wire is the biggest consumer of pure copper and, as a result, copper wire production uses little copper scrap. The remaining copper market, including copper roofing, contains 75% recycled product. Almost 50% of this is post-consumer recycled product.3
Zinc Recycling
Over 30% of zinc used in all applications worldwide comes from recycling. That percentage is expected to increase.4,5 In building applications, especially in Europe, more than 90% of old, rolled zinc products are recovered and generally recycled into other types of zinc products.
An estimated 13 Mt of refined zinc metal is produced annually. Of this, 12 Mt comes from ores and concentrates while the balance is supplied from old scrap that requires refinement before reuse. The total amount of zinc consumed annually is approximately 16 Mt. The 3 million ton gap is supplied from secondary or recycled sources that do not require further refinement prior to reuse. This category is made up primarily of alloys (brass and die castings) and zinc sheet, which are simply re-melted.7
The average recycled content of refined metal zinc in building products is estimated to be 15%.6 However, the total recycled content of zinc, including all potential building applications (alloys and rolled zinc), is approximately 25%.
For zinc, the End of Life Recycling Rate is the preferred measure as it quantifies the amounts of zinc actually recovered at the end of product life (“old scrap”) and recycled into new zinc metal. This measurement requires an understanding of historical production and consumption levels, product lifetimes, and collection rates. It is estimated that 60% of available zinc at the end of life is recovered and actually recycled.6
Conclusions
The high recycled content and recyclability of metals like steel, aluminum, copper, and zinc allow for metal construction products to be routinely included on listings for “green” or sustainable building materials.
The USGBC LEED green building rating program recognizes the importance of the weighted, total, and recycled content of a building project’s materials. The use of recycled metal can help a LEED registered building project acquire points in many credits within the program. MR
References:
1. www.steelsustainability.org
2. The Aluminum Association LEED Fact Sheet (www.aluminum.org)
3. Copper Development Association (www.copper.org)
4. International Zinc Association (www.zincworld.org)
5. “UM Recycling Workshop,” Report of proceedings, Brussels, June 10, 1999.
6. “Zinc Recycling – Closing the Loop,” International Zinc Association, 2011, www.zinc.org
7. “Le recyclage des métaux non ferreux” (Recycling non-ferrous metals), M.E.Henstock, Publication of the Conseil International des Métaux et de l’Environnement, May 1996
Insights From a Recycler
By Linda Schmid
In 2022, Kripke Enterprises sold 190,000,000 pounds of recycled metal, so there is a whole lot of recycling going on. According to Alan Sallee Jr., Sr. Vice President of Sales, their facilities collect old aluminum rims, scrap radiators, catalytic converters, old dishewashers, old sheeting from buildings, and more.
Scrap aluminum is sorted into different grades and is resold as recovered secondary ingot (a recycled solid mass of high purity aluminum) or sent to the extruder for extrusion.
The wonderful thing about metal is its recyclability. While extraction of aluminum from the ground along with processing and refining is very costly and requires high energy consumption, recycled aluminum is around 92% more efficient. Further, it doesn’t lose any of its inherent strength or performance qualities so it can be recycled over and over again.
Primary steel is created by forcing oxygen through molten iron ore, thereby “oxidizing it and turning it into steel. Secondary steel can be made from scrap iron or scrap steel which is melted down in an electric arc furnace. Secondary steel production is about twice as efficient as primary production.
Sallee says the steel they collect is resold, and put through that reclamation process, turning it into new steel. He estimates that about 90% of the steel purchased is recycled.