By Charlie Smith, McElroy Metal
Reroof over existing or remove and replace? That is a question that has to be answered with every metal roof that has reached the end of its service life. Whether the existing roof is a 36” wide exposed fastener panel or a standing seam installed over open framing on a metal building or over solid decking, you have a choice whether to recover the existing roof or remove and replace. Many factors need to be considered when making this decision, including the sensitivity of the occupant to disruption, the role the existing roof system plays in stabilizing the structure, the difficulty of removing the existing roof, whether the existing roof is installed over a solid deck or open frame, the capacity of the existing structure to carry more weight, the owner’s desire to add insulation, the underside appearance, and the condition of the purlins or deck, to name a few.
When assessing occupant disruption, a main consideration is determining if the existing roof is installed over a solid deck or on open purlins. If a solid deck, the disruption of remove and replace and associated waterproofing will be miniscule in comparison to an open-frame structure. If the existing roof is installed on a metal building with open framing, then recovering the existing roof reduces the risk of flooding the building and minimizes disruption to the occupant. Removing and replacing a roof on one of these structures will most likely result in having large sections of the building open and exposed to the weather during the process. This is partly due to the ever-increasing design wind pressures and snow loads imposed by updated building codes. The new roof will need to meet the current loads, which will probably be significantly higher than the loads required when the original roof was installed. Higher design loads mean additional purlins may need to be added in the perimeter, corner and snow drift areas. Fortunately, with recover, there are ways to meet these increased loads without adding purlins. Contractors and building owners need to be aware that if the roof is removed, adding or replacing purlins means opening the building over an entire bay which can leave a hole over 30 feet wide in the roof. This hole may be impossible to open and close in one day, depending on panel lengths and penetrations. This is one reason that recovering the roof on a metal building is often the best alternative.
The two most common types of metal roof systems being used today are 36” wide sheets installed with exposed fasteners and free floating standing seam systems that are installed with concealed clips and fasteners. The exposed fastener systems are fixed rigidly to the substrate and standing seams are free to expand and contract as the temperature changes. The most common exposed fastener panel is called an R-panel with major ribs that are 1¼” tall and 12” on center. On a metal building, the R-panel is attached to every purlin 6” to 12” on center in horizontal lines typically 5’ apart. They are also attached at the side lap every 3’ in a vertical line 6” to 12” on center. On an open-frame metal building, this type of attachment is critical to the building design. In simple terms, the roof panels are stabilizing the purlins and holding the building square. If you remove an existing exposed fastener R-panel on a metal building and replace it with a free floating structural standing seam, you may end up with a king-sized problem. For this reason, it is almost always better to recover an existing R-panel if the intent is to replace with a standing seam. R-panels can be replaced in kind, one or two panels at a time or, if you want to replace an R-panel with a standing seam, you will most likely need to add bridging, bracing, or strapping between the purlins to stabilize them. A qualified engineer needs to look at the structure and determine the best way to stabilize the purlins.
Some roof panels are very difficult to remove while other panels come right off. The easiest panels to remove are exposed fastener panels. As outlined above, you may have to be careful about doing it, but a crew can remove a lot of exposed fastener panels in a day. Snap together and single-lock standing seam panels are relatively easy to remove. Double-lock standing seams are very difficult to remove and require a seam cutter to get them off.
In general, based on interruption, ease of removal and the existing roof’s role in stabilizing the structure, here are some scenarios and suggestions:
One of the biggest concerns about recovering an existing roof with another metal roof (particularly on a metal building) is the additional weight of the new roof. The International Existing Building Code has a section that addresses adding a new roof on top of an old roof. In section 707, the code states that during reroofing, the building structure must be brought up to the current code. One of the exceptions to this rule is a second layer of roofing may be added as long as it weighs less than 3 pounds per square foot. There are at least seven ways to recover an existing metal roof with a new metal roof and they all weigh less than 3 pounds per square foot. There are also ways to increase the load carrying capacity of metal building purlins while reroofing over certain types of existing roof panels. There has been a lot of testing done recently and papers written over the past couple of years on metal building strengthening while doing a retrofit. I am currently working on a job where recovering the roof actually added 7 pounds per square foot of load carrying capacity to the existing structure! Most people are concerned about adding weight to their building when the fact is, in many instances, the structure is being enhanced by adding a second layer of roofing. The bottom line is that it is always a good idea to have an engineer that specializes in metal buildings look at the structure to make sure the building is suitable for recover.
The IECC (International Energy Conservation Council) mandates that any time a roof is removed and replaced on a building where people live and work, the new roof must meet the current insulation requirement. Usually that is R-30 which is around 5” of rigid polyiso or 9” of batt. One thing is for sure: Adding 9” of batt insulation in an existing metal building can be extremely challenging, especially where there is a lot of bracing, piping or conduits between the purlins. Also, there are very few standing seam panel clips that will accommodate that much batt over the purlins. On a traditional building with a solid deck, adding rigid insulation is easy, whether the existing roof is removed or left in place and recovered.
There are a couple of exceptions to the requirement to bring the insulation up to code during reroofing. One is to leave the existing roof in place and to cover it with another roof. Recovering puts the owner in charge of how much insulation he wants to add to his building. There is an air space formed between the two roofs that can be filled with batt or rigid insulation. This air space can also be left open and ventilated. A ventilated air space between two roofs can greatly reduce the heat transfer from the outside and the only additional cost is the perforated metal trim at the eave and ridge that allows air to pass between the two roofs. Finally, if the owner is planning to be there a long time, a great way to remove and replace on a metal building is to remove the existing roof panel and insulation down to the purlins, then install a 26 gauge liner panel on top of the purlins, add the required thickness of rigid insulation on top of the liner, then high temp peel and stick followed by a structural standing seam on top of the iso attached through to the purlins. This eliminates the batt insulation and vinyl backer and replaces it with a nice clean white metal ceiling. This system also eliminates the thermal bridging associated with compressed batt over the purlins.
Many existing metal buildings have interior appearance issues where the batt insulation is full of holes, sagging or hanging down from the ceiling. Normally that dictates the roof has to come off to replace the insulation. That is easy enough to do if the existing roof is an R-panel and the plan is to replace in kind. If the existing is an R-panel and the plan is to replace with a standing seam, adding bracing to stabilize the purlins may be required. If there is easy access to the underside of the roof, one solution is to leave the roof panels as they are, cut the insulation out from the inside then install anther R-panel or standing seam over the top of the old roof. Insulation can be added between the two roofs or just ventilate the resulting air space. That ensures that the building structure is not disturbed.
Typically, if purlins in a metal building need to be added or replaced, the existing roof has to come off. There are instances where this work can be accomplished from the underside, but most purlin addition or replacement is done from above. There are two reasons to add or replace purlins in a metal building: One is that they are no longer serviceable. This can be due to corrosion or damage and typically involve the eave strut. The other is the requirement to add purlins between the existing purlins to meet the current wind or snow loads. This can be done to beef up the building structure or to increase the roof system wind uplift capacity by providing more points of attachment. If the purpose of adding purlins is to enhance the roof system, this work can be performed on top of the existing roof by assembling a “grid system” and attaching it through the old roof into the structure below. Grid systems can add considerably to the cost of doing a retrofit, but greatly reduce the interruption to the occupant.
Each re-roofing job presents its own challenges and opportunities to solve problems that best suit the owner’s objectives. The default position is normally to remove and replace the existing roof and the recover option is often overlooked. Recover is often the best solution for many jobs. MR
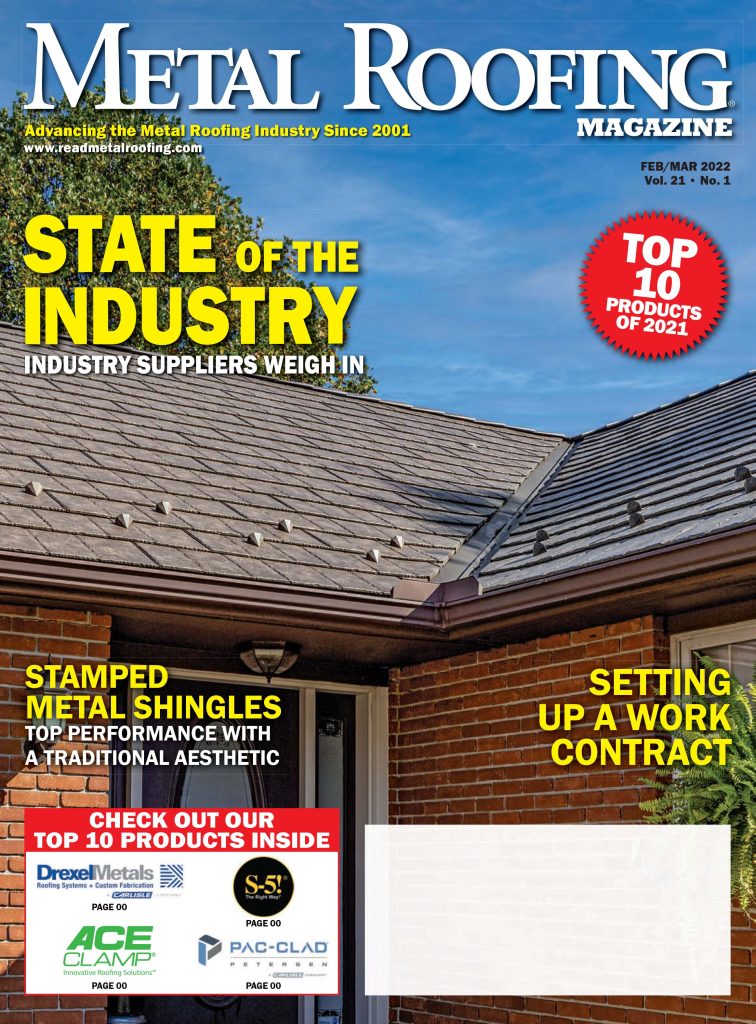
Sign Up For A Free Subscription
Anyone who is involved in the construction trade is welcome to sign up for a free print or digital subscription to Metal Roofing Magazine, which has been advancing the metal roofing industry since 2001. This go-to resource for metal roofing professionals is published 7 times per year.