DripStop’s Tony DelGhingaro answers common questions about condensation control
Tony DelGhingaro has been working in the building industry for over nine years focusing on condensation control in metal buildings. He works with roll formers, builders, contractors, & salespeople, as well as other industry professionals. He feels he, “could not have asked for a better product to be associated with than Dripstop™.” The first thing Tony learned is that condensation is tied directly to ventilation—or the lack thereof:
“While I have a great understanding today, I continue to learn and share best practices. Even though condensation control membranes were not new in 2013, most of the people I met in the beginning, were not sure what it was, and they really did not know how it worked. This provided a great opportunity for me to share the knowledge I had and offer different solutions. I have had a great time traveling across the US and Canada meeting and working with such a diverse group of building professionals. It allows me to share best practices learned in one place and bring them to a completely different geographic region.
“The best part of my job is watching my customers grow their businesses; and I’m happy to say that, after nine years, I can no longer keep track of all the different success stories. I like to think DS has played a role in that growth.”
Q: How large of an issue is condensation perceived by post-frame building consumers?
A: Unfortunately, it is often overlooked by consumers until it becomes a problem. Many initially think their roof is leaking; only to find out later it is condensation that is dripping from the bare metal above.
Q: What actually causes condensation to occur?
A: Warmer wet air touches a cooler surface and moisture falls out of suspension. The difference in temperature and the dew point determines when water vapor becomes liquid. An easy example most everyone is aware of is the ice-cold glass sitting on a table; the same thing happens inside a building where the warm humid air rises and hits the colder metal roof.
Q: How does it impact a post-frame structure?
A: If the condensation is allowed to clear, or if it can be prevented altogether, then there is almost no impact. However, if nothing is done, the results could be anywhere from water damage to contents below to mold & rot forming on purlins. Essentially, it could be like having it rain inside the building.
Q: What are the options builders have for dealing with the issue?
A: I always start by saying EVERY building needs ventilation. With that in mind, I believe there are two different ways to deal with condensation. The first way builders remedy the problem is with insulation. The idea here is to prevent the temperature difference from happening at all. The other way is to use a condensation control membrane; like DR!PSTOP! This option captures the moisture overnight and clears it the next day.
Q: Are there cost differences in the remedy method/materials selected by the builder?
A: Compared to not doing anything, which happens more than the building industry would like, there is an additional cost to both options. Since insulation requires additional time and labor to install, there is an added cost on top of the purchase price of the insulation. Products applied at the same time the metal panels are produced and arrive on the jobsite already installed, eliminate the additional time and labor costs.
Q: What is the impact on a builder’s customer in terms of longevity?
A: I believe both options above can be great solutions for long periods of time; especially when installed to manufacturers’ specifications. With some membranes, the customer even gets a maintenance free option with a 20-year warranty.
Q: Are there variable installation time impacts involved for the builder?
A: With a condensation control membrane, there is no additional time or labor to install for the builder. However, insulation does require additional time and labor hours.
Q: What is the biggest issue that arises that causes a repair to be needed? Is there a way for a builder to minimize the issue from occurring?
A: If nothing is used and condensation is allowed drip down, it can be quite costly. Obviously, it depends on what is being stored below. I have also seen older buildings without adequate ventilation with plenty of mold spots and darker areas and rot on the purlins. Over time these may need to be replaced. Using a membrane prevents the dripping and further damage from moisture.
Q: What do builders need to teach their customers about maintenance checks regarding moisture control?
A: Another tricky question. Personally, for general maintenance, I would recommend a building owner do a visual inspection of the entire building at least a couple times a year, inside and out. Look for any changes (water spots, darker areas, or structural changes) in the roof line, the doors & windows, the ceiling, or framework above, along with the floor and any drainage systems. For new buildings, I would suggest the same after heavy winds and storms the first year or two.
Q: What is important to know about ventilation?
A: In my experience, this is probably the most confusing or misunderstood part of the building / process. I have been in too many buildings that claim to be vented – only to put a meter at the ridge and see ZERO air movement. This is the single biggest cause of moisture and condensation problems inside buildings. Venting a building is similar to us breathing, where proper airflow makes everything healthier. Regardless of using bare metal, insulated metal, or metal with a condensation membrane — just like people, ALL buildings need to breathe! MR
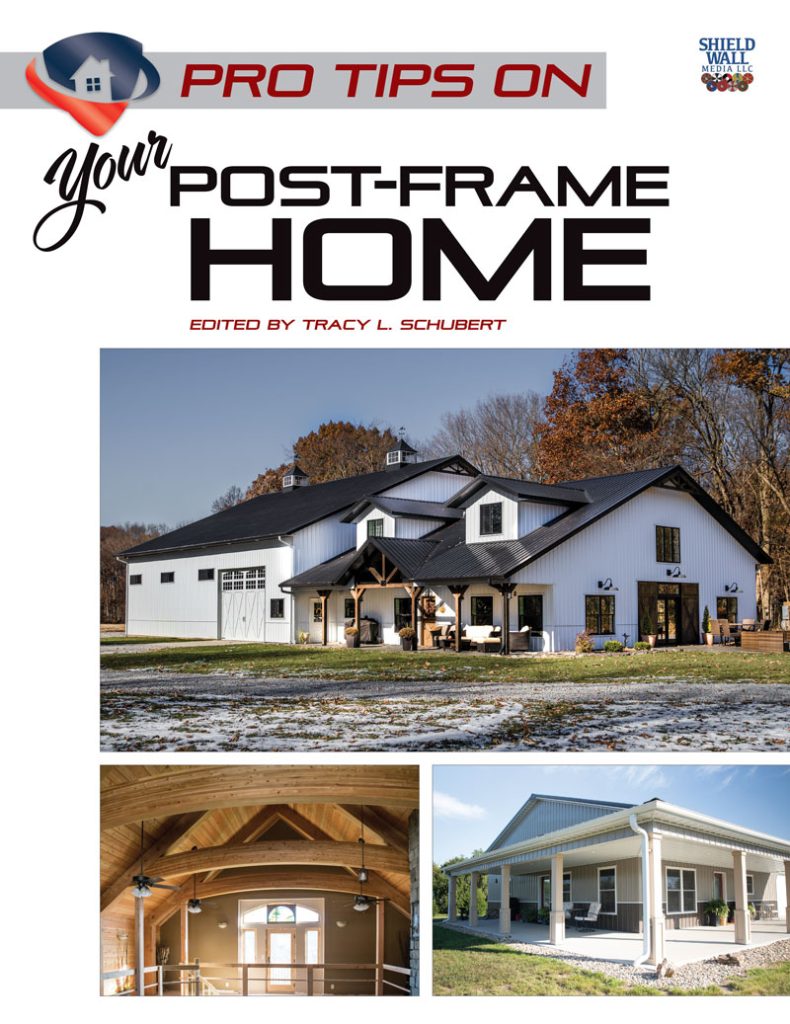
5 Pro Tips that will benefit your customers:
1 – Ventilation is important to the function and longevity of their build. Explain how ventilation relates to human breathing for an easy demonstration.
2 – Consider what will be stored in their new building so you work together to pick the right type of moisture control for their needs.
3 – Provide a time/cost estimate for the insulation install for the consumer to consider against the cost of a moisture control membrane.
4 – Make sure customers clearly understand what is warranted by the builder and what is warranted by the manufacturer.
5 – Make sure your customers know what to look for to maintain their building and who to contact if they have an issue.
The popularity of post-frame homes is growing. Help your potential customers understand why they may be a better choice than a traditional stick-built home. The brand new Pro Tips On Your Post-Frame Home is available exclusively on Amazon: https://tinyurl.com/25aev5n7.
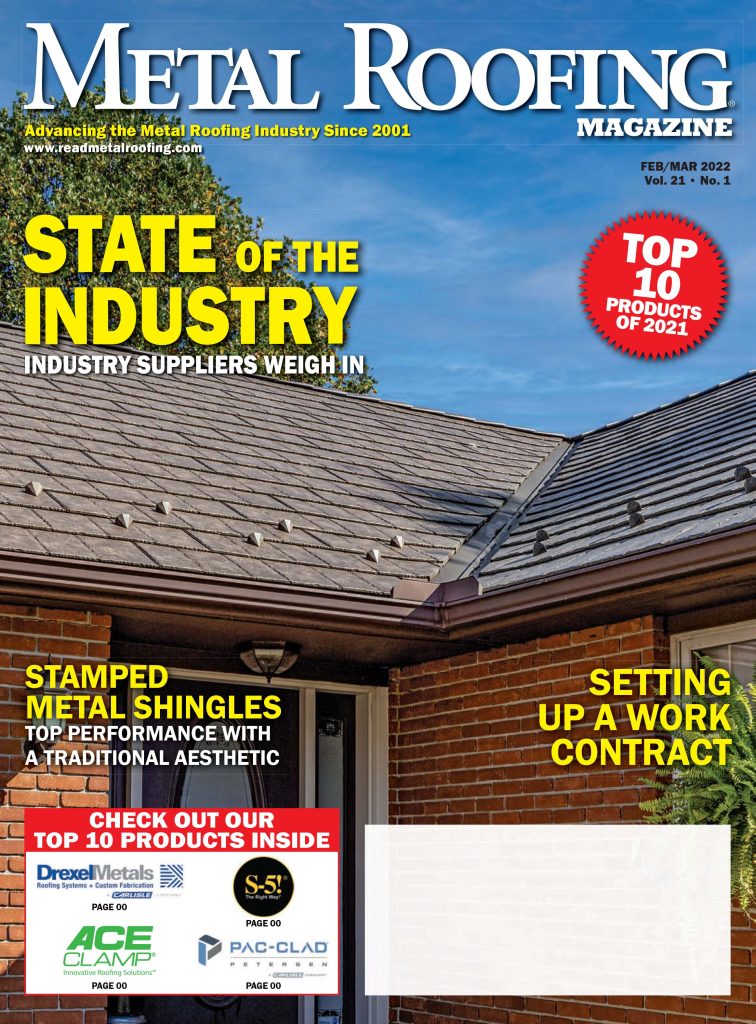
Sign Up For A Free Subscription
Anyone who is involved in the construction trade is welcome to sign up for a free print or digital subscription to Metal Roofing Magazine, which has been advancing the metal roofing industry since 2001. This go-to resource for metal roofing professionals is published 7 times per year.