By Shawn Huffman, Beck Automation
What do you think of when you hear “inventory management”? For many, it’s making sure they know how much coil inventory they have on the floor. In today’s market, that is only a small piece of a bigger picture. Inventory management consists of not only your raw coil inventory, but how that material is being used. For example, how much scrap is being produced? What is causing you to create scrap? What changes can be made to reduce scrap?
With today’s technology in both Controls and Office-to-Shop software, seamless plant integration can be accomplished, giving management the tools required to answer not only these, but virtually all of your questions—allowing you to make changes that can affect the bottom line.
Whether you’re in the market for a new machine or interested in upgrading your current equipment, it’s important to make sure you will have the capability to get what you want out of your business. This is where insight and forethought can make a world of difference to both your efficiency and bottom line.
Machine Concept and Configuration
Is your machine configured to help reduce scrap? There are many different configurations of machines. Three basic concepts are: Pre-Cut, Post-Cut, and Pre-Punch/Post-Cut. Each of these has their own potential issues that can generate unwanted scrap. However, by understanding what the issues are, there are some simple options that can help overcome each.
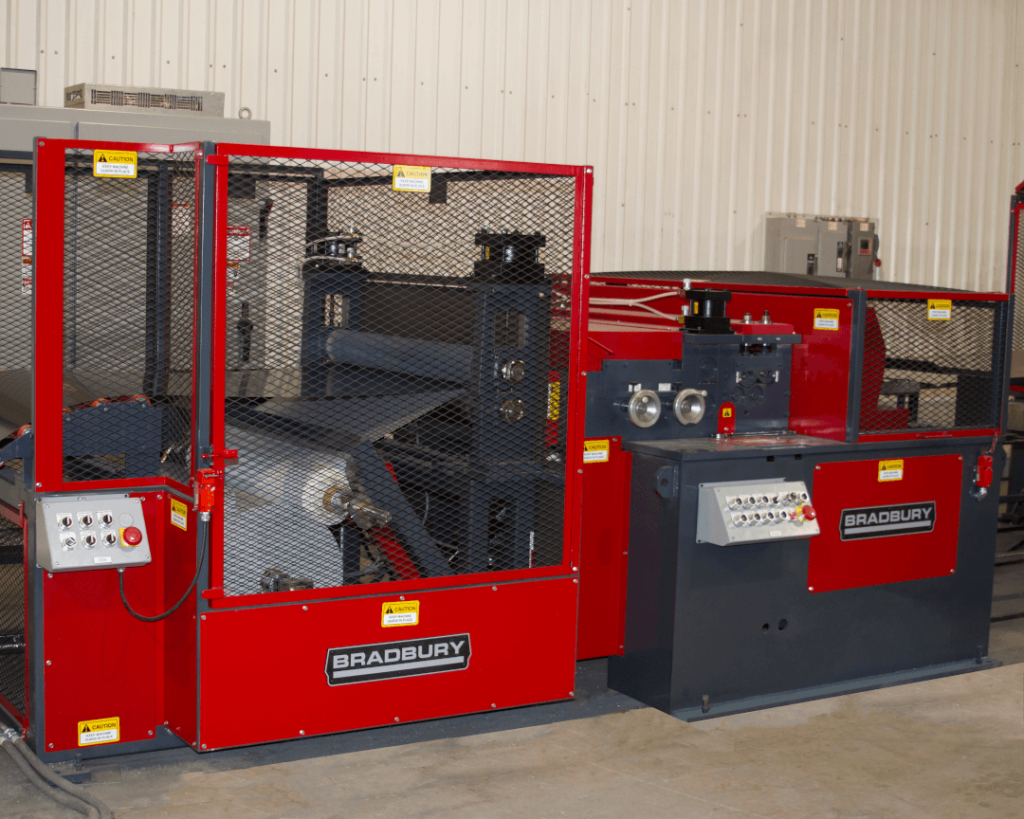
Pre-Cut Lines
are generally low scrap producers. However, one shortfall is the ability to produce shorter pieces. With a controller capable of auto-joining pieces that are too short to run through the roll former, operators can run these shorter parts, which are joined together and can then be taken offline and sheared down to the correct length. As with all lines, another way to reduce scrap is by reducing coil changes. New controls have the capability to run jobs based on like materials and/or profiles. This not only reduces scrap associated with changeovers, but will also reduce downtime associated with loading a new coil.
Post-Cut Lines
generally create scrap upon the tail out of a coil due to a coil change being required, but the machine is still full of unused material. With a Smart-Cut feature, prior to a material change being required, the line will halt and notify the operator to cut the material loose, ensuring there is enough material in the machine to complete the remainder of the order. Adding a pull-across or powered shear can ensure the last piece is the correct length and no scrap is produced.
Pre-Punch/Post-Cut Lines
generally create scrap either on thread up or tail out of material. Adding an additional encoder (one at the entry end and one at the exit end) can eliminate scrap. The additional encoder in conjunction with a “Thread” or “Slow Run” mode can allow the operator to jog material through the machine while producing good parts. When the material reaches the shear, it will crop the leading edge, resulting in only minimal scrap. By switching to the exit end encoder after the material reaches the shear and performs the first cut, the last piece of material will be tracked all the way to the shear, resulting in minimal scrap as well.
Modern Controls
Are your current controls providing you with the capability to track your production and scrap? The process of the operator manually tracking coil and submitting this documentation to the office staff for manual entry into your ERP is long gone. With modern controls and software packages, you can have complete integration between the office and your machine(s).
One crucial aspect of reducing scrap is making sure you are using the correct coil. Coils can be scanned into the controller, and validation can be accomplished by verifying the coil loaded on the machine is the correct material required for the job. Upon pressing line start, the controller will perform a check to validate the material assigned to the coil matches the material required for the job. The validation can either appear as a warning, notifying an operator that incorrect material was loaded and giving them the ability to run anyway in case a substitute is required, or force a supervisor to enter a password acknowledging the substitution is being made.
Material detect switches will also ensure that scrap is being reported correctly. When threading up a new coil, the Length Past Shear is automatically reset to a negative number (shear to encoder distance) and will count down to 0.00″ once the coil reaches the shear, ensuring the correct scrap is reported. Likewise, on tail out, the line will halt, allowing the operator to acknowledge if the last piece was good or scrap, and reporting back the correct amount of scrap that was produced.
Modern controls have additional benefits such as Profile/Level selection to ensure that the correct level is running on a dual level line for the profile needing produced, requiring the operator to perform quality checks at specific intervals to make sure the parts are correct and within tolerance, and employee login to hold employees accountable and verify who is running the machine(s).
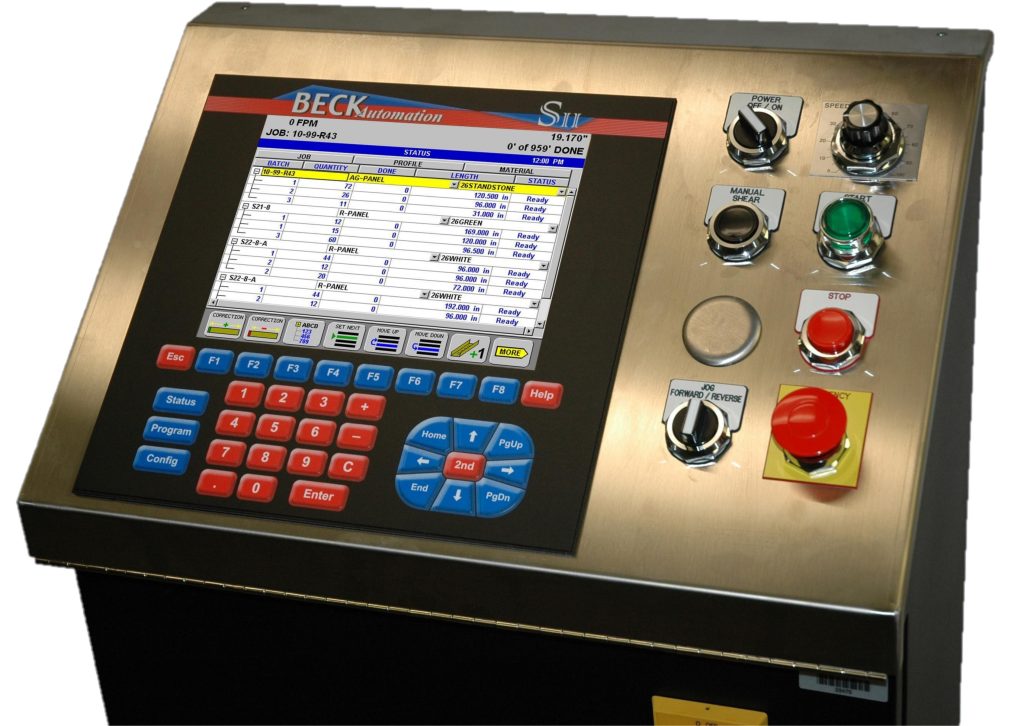
Office-to-Shop Software
Integration
Implementing an office-to-shop software program allows all events on your machine(s) to be tracked. This is where software can give management a leg up. They can evaluate overall scrap production and trace it back to the root cause. As scrap is created on the machine, operators can select from a list of scrap reasons, assigning the scrap to the specified reason. This information can be evaluated, giving management the necessary tools to take corrective action.
Integrating the software directly with your ERP or design software can also reduce errors by entering information one time. This not only saves the wasted time of double entry, but will also eliminate entry errors, which can prove costly to your customers and your bottom line. This integration can be bidirectional, so the orders are not only being sent to the office-to-shop software for production, but data can be pushed back to an ERP software for tracking order completion, relieving coil inventory, and even tracking man hours.
Production/Coil Tracking/Management Evaluation
While the ultimate goal is to reduce scrap, you first need to know what is generating the scrap. There’s no use purchasing coil from a new vendor if 90% of the scrap is generated due to material handling. In this case, your efforts would be better realized if you reduced coil changes or trained staff on the handling of coils.
The ability to run reports with accurate data gives management the information necessary to find issues and take the necessary corrective actions. Management can drill down into the data to find details such as how much scrap is being created, what is generating this scrap, how much downtime is being experienced on each machine, and what is causing the downtime. This allows management to take the necessary corrective actions on what can have the biggest effect, ensuring money is being spent on what will provide the best ROI.
Reporting which coil is being used and reconciling the used footage back to the correct coil is important for knowing your current inventory, and also for future warranty claims. Being able to track what coil was used will enable your company to issue claims and work with vendors to reconcile these claims. If/when issues do arise, you can be confident in knowing how and when the job was produced, who was running the machine when the job was produced, and what exactly was produced.
Management Evaluation
KPI’s (Key Performance Indexes) can be displayed via monitors and provide real-time data on what is most important to your company. These indexes can usually be customized and display the information in a format that meets your company’s needs and can include machine efficiency (OEE) as well as scrap, downtime/run time, and daily or hourly production, and can be related to goals set for each machine. These not only provide necessary information for management but can also be used to create a competitive spirit among operators, which can also increase productivity.
Preventative maintenance will also ensure the machine is running at its full potential and the end product meets the specifications. The benefits of preventative maintenance are keeping downtime to a minimum, which increases production, in turn increasing profits while keeping your customers happy by providing on-time deliveries. This can include a multitude of tasks from greasing components, to sharpening or replacing dies and blades, to refinishing or replacing roll tooling. Since machine manufacturers all have different recommendations as to when this work should be performed, it can become quite cumbersome to create a procedure to make sure everything is being maintained correctly and on time.
With today’s technology, your machine can notify both maintenance personnel and management when specific preventative maintenance is due, past due, or has been performed. This can adhere to the manufacturer’s specifications, whether it’s based on time, lineal footage, or number of press cycles. Once the maintenance staff is notified that a procedure is due, they can also easily pull up how the task needs to be performed, whether it’s basic instructions, pictures, or even a video. It can also tell maintenance personnel how long it should take to perform the task. By providing staff with all of the information they need to complete a task at their fingertips, it is more likely it will be completed correctly and on time.
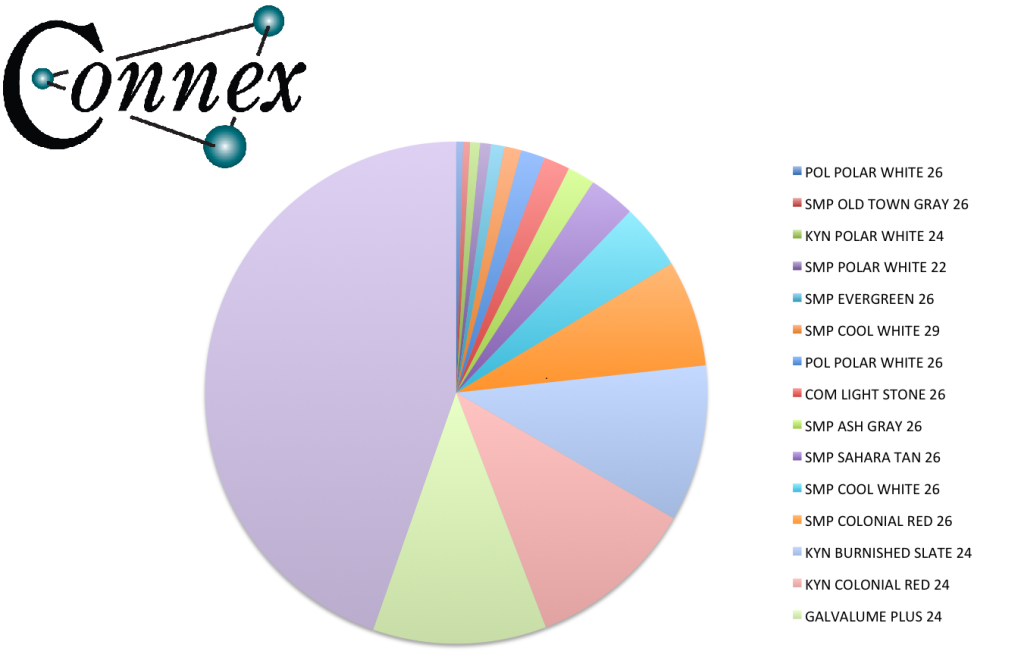
An added benefit of having preventative maintenance in a database on a computer is being able to easily track what has been performed, when it has been performed, and how long it took to perform it so there is an accountability that is provided. Management can easily track what has been performed and what is coming up, which also helps them schedule around production. Trends can be seen so corrections can be taken. With knowing how long it will take to perform preventive maintenance, a schedule can be put together that can be mixed in with production, upgrades, and modifications to equipment.
The final aspect is getting the product to your customers by keeping track of your shipments and deliveries. Modern software allows you to schedule shipping dates, set routes, and verify both the loading and unloading of shipments. This helps by preventing orders from being sent to the wrong customer, stops employees from forgetting to load portions of an order, and ensures delivery with a received signature and/or photo verification, efficiently taking logistic control of your outbound products.
If you truly want to fully integrate your inventory management with your roll forming business, it is necessary to evaluate your needs, be informed of what options are available, and utilize the technology available to achieve your needs. MR
For more information, visit www.beckautomation.com.