The following white paper was written for the Metal Building Manufacturers Association and reprinted with their permission.
By Brian Gardiner FRCI, RRC, CCS
BMG Enterprises, LLC
The goal of this paper is to compare two commonly used methods of retrofitting existing metal roofs and illustrate important design considerations that frequently apply to candidate buildings. As this is a limited review, not all considerations will apply and additional items not addressed, such as the potential for condensation, can prove important to evaluate for a successful retrofit.
Why Retrofit?
Metal roofs have been documented to perform well and have a long service life. However, when an existing metal roof does reach the end of its service life, or is experiencing problems, it can either be repaired, reroofed, or retrofitted. Retrofitting (aka recovering) has many advantages over reroofing, including:
Original roof provides temporary building interior protection during new roof installation
Allows for building operations to continue
Reduces landfill waste
Reuses existing insulation and allows adding more insulation over the existing roof
Provides a safer work surface than exposed existing secondary structural members
Reduced cost
What are the Retrofit Options?
Typically, a compact (low-profile), lightweight (less than 3 pounds per square foot) retrofit solution is recommended for metal building systems, as the original structure may have been optimally designed using a lightweight metal roof. The existing building’s structure may require enhancement to meet the current building code and to function properly for the selected retrofit roof system. Two common retrofit options that are the subject of this paper are:
Metal over Metal
Usually another lightweight metal roof is installed over the existing metal roof [Figure 1]. Metal roof retrofits do not typically rely on the existing metal roof to function as a structural deck for support and attachment of the new metal roof system.
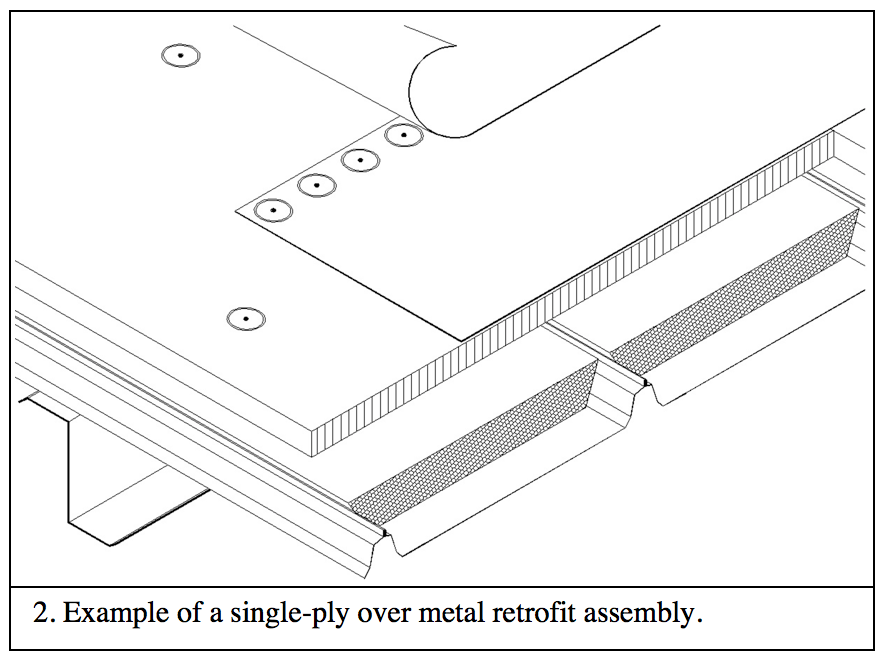
Single-Ply over Metal
Single-ply roof systems are also lightweight and utilized for retrofits over existing metal roofs [Figure 2]. Many single-ply membrane roofs rely on the existing metal roof to function as a structural deck for support and attachment of the roof system, including board insulation, as well as for support of live, snow, and wind loads, and for providing stability to the roof support members.
What are the Building Code Requirements?
The International Building Code (IBC) and the International Existing Building Code (IEBC) have provisions on reroofing. Check with the local building official to determine which code is applicable. In either case, according to Section 105.2 in both the IBC and IEBC, reroofing is not exempt from permit requirements.
In the 2015 IBC, Section 1511 pertains to reroofing, including roof recovers, but the provisions are limited. Section 1511.1 states that materials and method of application used for recovering shall comply with the requirements of Chapter 15, which governs the design, materials, construction and quality of roof assemblies. Section 1511.3.1 specifically addresses metal roof retrofits: “Complete and separate roofing systems, such as standing-seam metal roof panel systems, that are designed to transmit the roof loads directly to the building’s structural system and that do not rely on existing roofs and roof coverings for support, shall not require the removal of existing roof coverings.”
There are more provisions in the 2015 IEBC that apply to reroofing, including the existing structure. The IEBC has three compliance methods, Prescriptive, Work Area, and Performance, which have different provisions. We will look at the Prescriptive and Work Area methods.
According to the IEBC, a roof retrofit would be considered an alteration (not a repair or an addition). Section 403.3 of the Prescriptive Method addresses existing structural elements carrying gravity load, stating the following:
Any existing gravity load-carrying structural element for which an alteration causes an increase in design gravity load of more than 5 percent shall be strengthened, supplemented, replaced or otherwise altered as needed to carry the increased gravity load required by the International Building Code for new structures. Any existing gravity load-carrying structural element whose gravity load-carrying capacity is decreased as part of the alteration shall be shown to have the capacity to resist the applicable design gravity loads required by the International Building Code for new structures.
Metal roof systems are typically lightweight, so 5 percent does not allow for a significant increase in gravity loads.
The IEBC Work Area Method is covered in Chapters 5 to 13. In Chapter 5, the classification of work is determined. Section 503 provides the scope of Level 1 alterations, which includes “. . . the covering of existing materials.” This section states, “Level 1 alterations shall comply with the provisions of Chapter 7.” Section 706 Reroofing is similar to Section 1511 of the 2015 IBC. Section 707 Structural applies when a reroofing permit is required, and includes the following from Section 707.2:
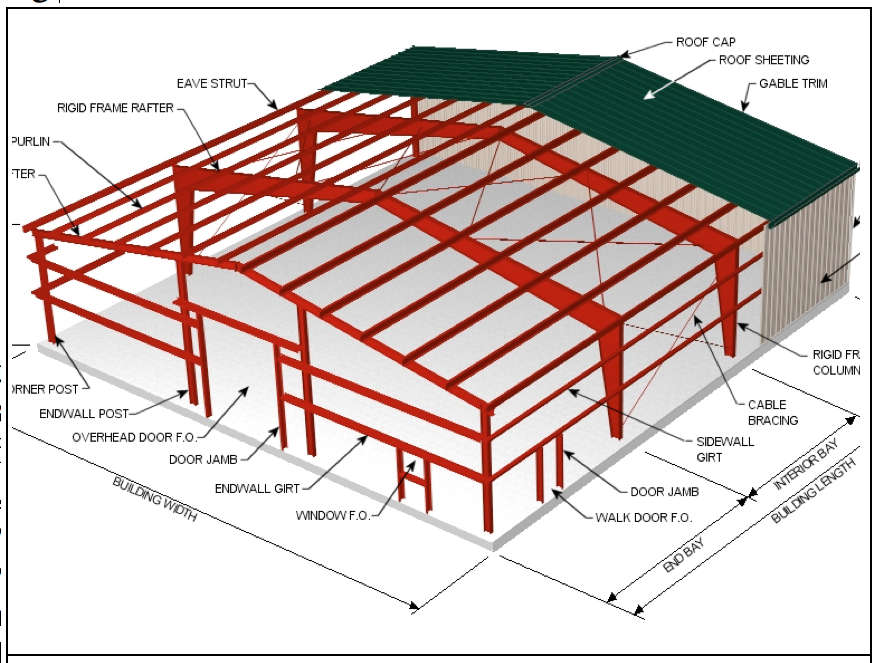
Where addition or replacement of roofing or replacement of equipment results in additional dead loads, structural components supporting such reroofing or equipment shall comply with the gravity load requirements of the International Building Code.
This provision has three exceptions, two of which are applicable to metal and single-ply retrofits:
1. Structural elements where the additional dead load from the roofing or equipment does not increase the force in the element by more than 5 percent.
3. Addition of a second layer of roof covering weighing 3 pounds per square foot or less over an existing, single layer of roof covering.
The first exception is similar to that found in the Prescriptive Method.
What are the Design Considerations?
Existing Support Structure
When designing a compact retrofit system over an existing metal roof, it is important to consider the age and type of structure that is being recovered, especially regarding what is typically utilized for new construction and how this differs from the retrofit situation. An existing metal building with cold-formed steel secondary structural members [Figure 3] and a 24 gauge, or thinner, metal panel roof is designed much differently than a conventional steel framed building with cambered bar joists and a 22 gauge, or thicker, steel deck.
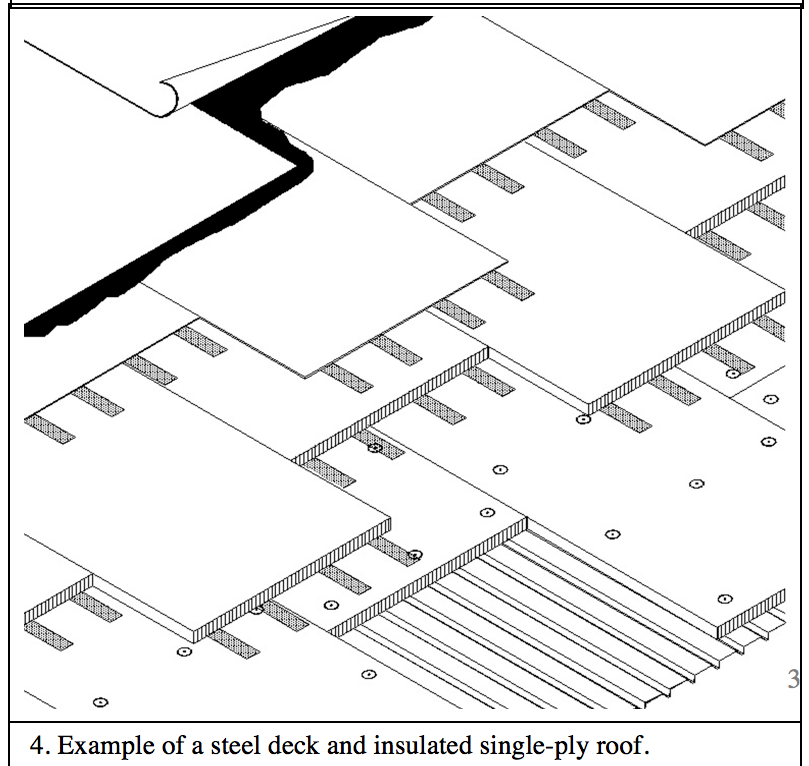
Conventional steel-framed buildings are typically built to support single-ply, modified bitumen, and built-up roof systems [Figure 4]. A metal building is typically not designed to accommodate a future retrofit roof system and due to multiple code changes since its construction, it may not meet the current building code’s wind and snow loads. Additionally, a metal building may have been designed using an earlier version of the American Iron and Steel Institute (AISI) Specification for the Design of Cold-Formed Steel Structural Members, AISI S100, with different strength limits and less comprehensive checks than are required in the current specification.
For any retrofit option, the existing support structure must be evaluated with regard to load path, strength, and serviceability. As noted above, the code requirements may necessitate strengthening or stiffening the existing support structure, because design loads in the later codes may have increased from the original design requirements.
Secondary Structural Member Deflection
The 2015 IBC Table 1604.3 ‘Footnote a’ stipulates a live load deflection limit of L/150 for secondary roof structural members that support only “formed metal sheeted roofing,” whereas the deflection limit when supporting a non-metal sheeted roof such as a single-ply roof is L/180 [Figure 5]. IBC deflection limits under snow loading and wind loading are identical for the two retrofit systems. Cold-formed steel purlins, often used as secondary structural members for metal buildings, are not cambered.
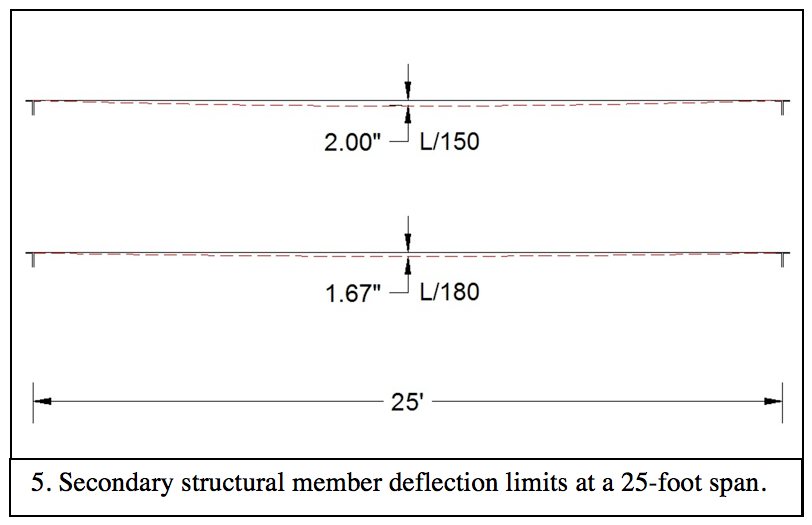
at a 25-foot span
The difference in deflection limits could require that the secondary structural members need additional stiffening for code compliance when a single-ply roof is used in a retrofit.
It is recommended that a licensed professional engineer practicing structural engineering with knowledge of metal buildings evaluate the existing structural system to ensure it is adequate for current building codes and to support the anticipated loads imposed by the retrofit roof system.
Existing Metal Roof Properties
Structural metal roofing is not the same as structural metal decking or steel roof deck. According to the IBC, structural metal roofing is where the metal roof panel functions as the roof deck, providing support for loads, and as a roof covering, providing weather protection. Steel roof deck, according to the Steel Deck Institute (SDI), is defined as steel deck panels used in a structural manner as a base for construction and supporting the roof insulation and membrane.
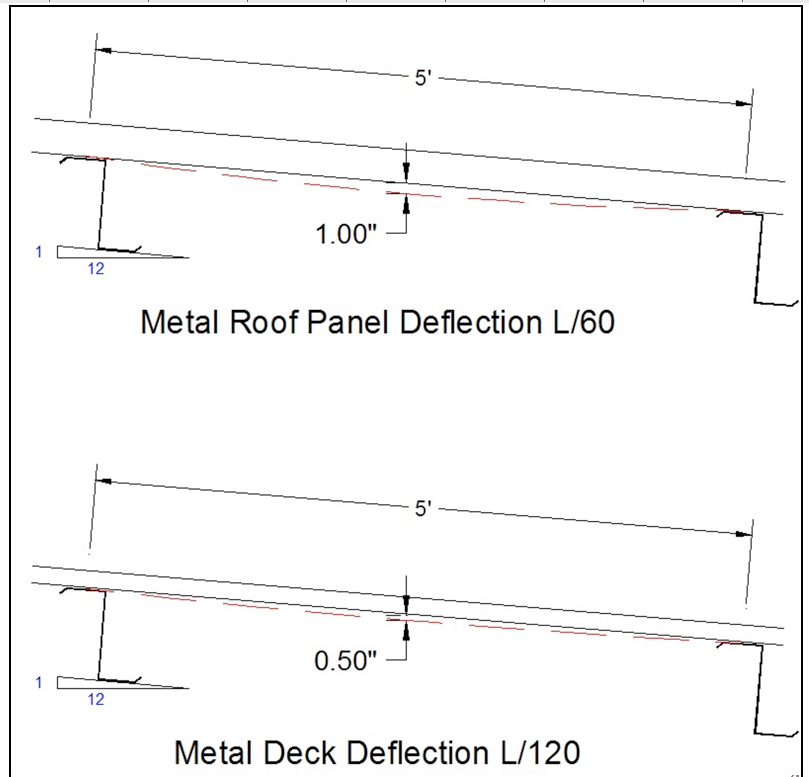
deflection comparisons
A single-ply roof system in new construction is designed to be integral with structural metal decking. Using an existing metal roof as the structural support system in a single-ply retrofit assembly changes many of the underlying assumptions and characteristics. For example, most of the wind uplift and fire ratings for single-ply roof systems are based on a 22 gauge, or thicker, steel deck. Steel deck profiles are typically thicker and more rigid that most metal roofs, especially standing-seam panels, which affect the strength and stiffness of the total assembly.
Existing metal roofs are typically 24 gauge, or thinner, steel and were not originally intended to perform as a structural deck for a single-ply roof system. The Steel Deck Institute’s ANSI/SDI RD-2010 Standard for Steel Roof Deck has a total load deflection limit for steel roof deck at L/120, whereas IBC Table 1604.3 ‘Footnote a’ stipulates a total load deflection limit of L/60 for structural metal roofing [Figure 6].
Single-ply roof manufacturers may also have minimum requirements for roof deck properties, depending on how the roof insulation and roof membrane are attached. Roof insulation or single-ply membranes that are adhered, rather than mechanically-attached, are more sensitive to excessive deflection. Therefore, the existing metal roof properties can be substantially different from the typical steel deck used with single-ply roofing. Less incompatibility exists between a metal over metal retrofit since the new metal roof has the same deflection limits and the load path is directly through to the secondary structural members.
It is recommended to consult with the local building official (authority having jurisdiction), a licensed professional engineer practicing structural engineering, and the single-ply roof manufacturer to determine if the existing building’s metal roof is adequate to perform as a structural deck for single-ply or other similar retrofit systems.
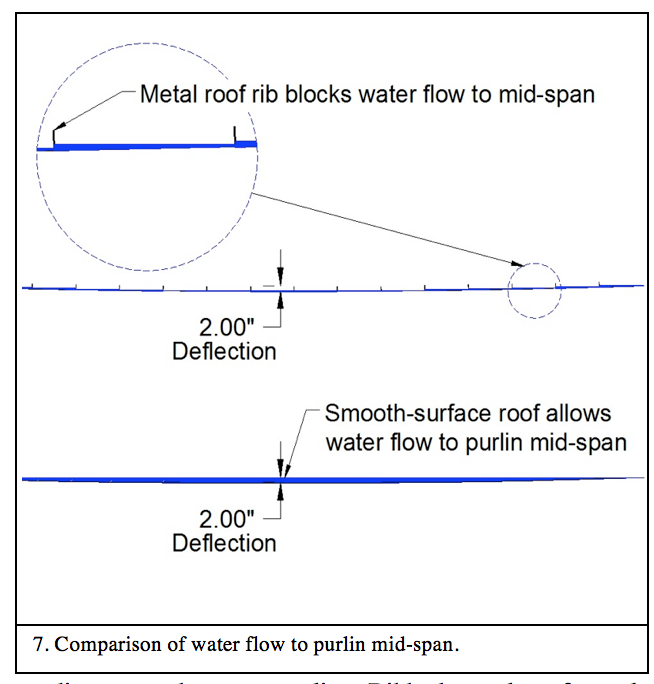
Ponding Water
The 2015 IBC Table 1604.3 states in ‘Footnote e’, “The above deflections do not ensure against ponding. Roofs that do not have sufficient slope or camber to assure adequate drainage shall be investigated for ponding.”
Most metal buildings with an existing metal roof panel at deflection limit of L/60 are sloped sufficiently to prevent ponding water between purlins. Ribbed metal roof panels control rainwater flow and do not allow lateral water movement to purlin mid-span locations where water ponding could progress into a significant problem. As a result, the metal building structural design may have been based on the assumption of a uniform load condition, especially in areas where little, or no, snow loads are anticipated.
A smooth-surfaced single-ply roof, on the other hand, does not control lateral water migration [Figure 7]. In addition, a mechanically-attached single-ply that billows or flutters during wind events may cause an unbalanced load due to water displacement. Unbalanced loads may occur when changing from a ribbed panel to a smooth-surfaced single-ply roof.
Building owners may add additional auxiliary, or collateral, loads to metal building secondary framing from the building interior non-uniformly, resulting in unanticipated excessive deflection due to unbalanced load that may deform adjacent existing purlins upward, sloping towards the excessive deflection [Figure 8].
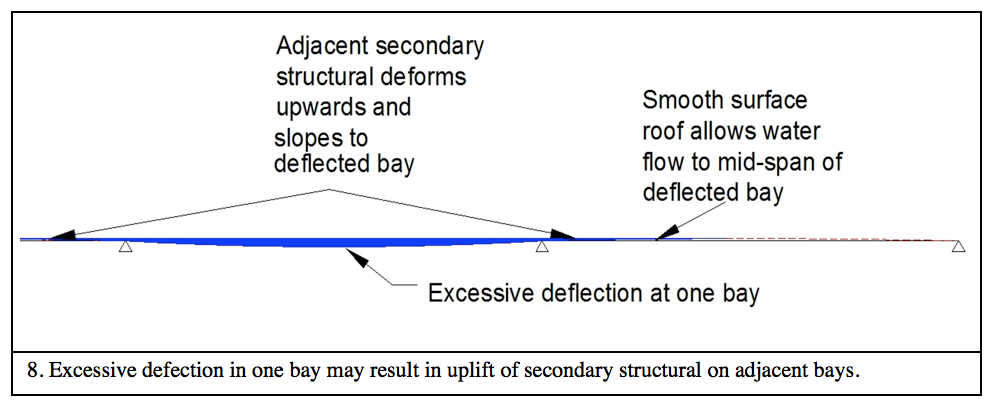
Deflection resulting in ponding water could be especially troublesome when an existing concealed gutter at a rise wall is retrofitted with either roof drains, or scuppers, that require a head of water on the roof surface to achieve the designed flow rate [Figure 9].
Ice and snow melt water could move laterally to the purlin mid-span on a smooth surfaced roof and pond due to differential thaw rates and be restricted from flowing off the roof by ice dams.
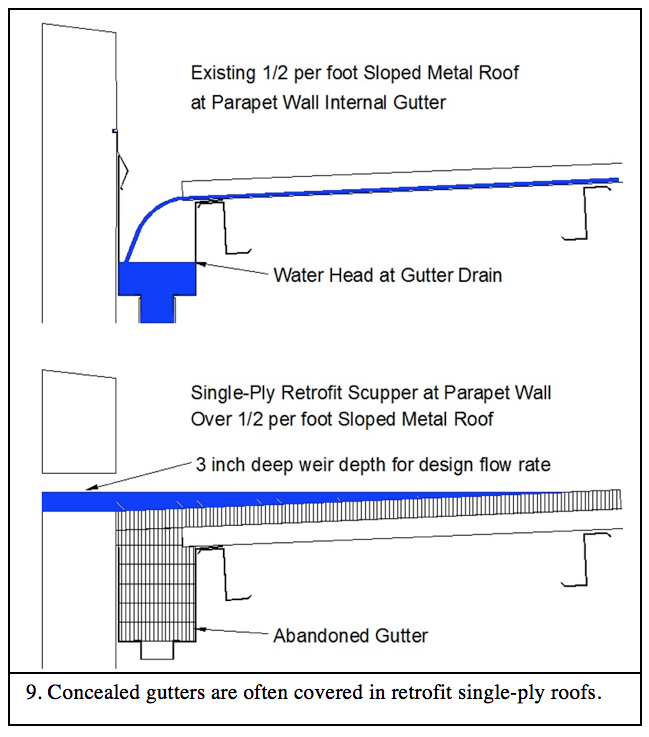
The 2015 IEBC 701.2 states: “Conformance. An existing building or portion thereof shall not be altered such that the building becomes less safe than its existing condition.”Installing a smooth surfaced roof that results in an unbalanced load condition could be construed as less safe than the original ribbed metal roof that prevented lateral water flow to the purlin mid-span. There are documented failures because of this issue.
It is recommended that a review of the building structure, the interior imposed loads, and drainage provisions be performed by licensed professional engineer(s) for unbalanced loads and potential water accumulation on a single-ply retrofit roof that may exceed the existing structural capacity.
Retrofit Roof Fastening
The capacity of the new metal roof panel and the existing metal building purlin thickness and spacing will usually dictate the spacing of the retrofit roof attachment.
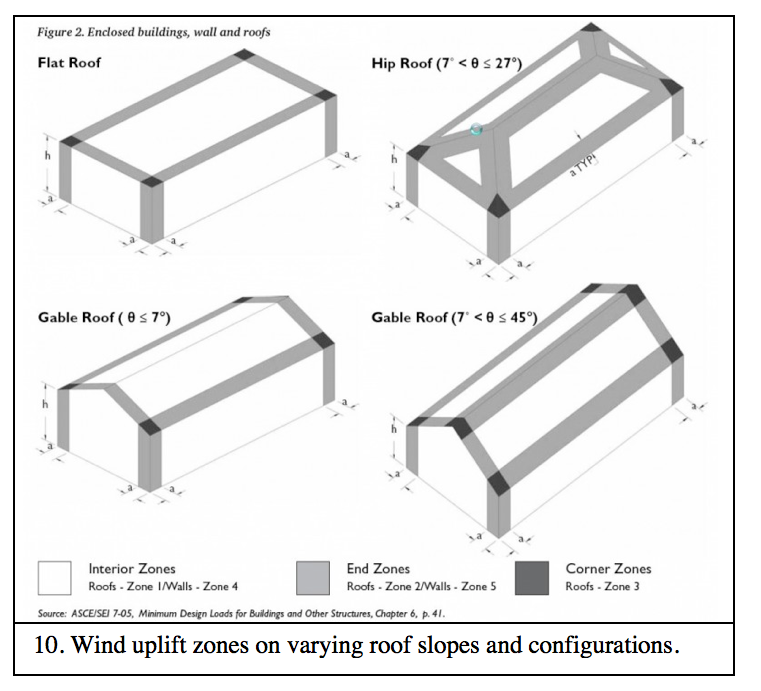
IBC references ASCE 7, Minimum Design Loads for Buildings and Other Structures, for wind load design. Design wind loads vary due to building height, geographic location, enclosed vs. partially enclosed, parapet height and other factors. Roofs have greater wind pressures in corner and edge zones. For steeper slope roofs, there are additional areas of greater wind pressures along the ridge [Figure 10]. As previously discussed, the latest code requirements may be substantially different, especially for wind loads, which have changed significantly over the past few decades.
Compact metal roof retrofits frequently incorporate secondary steel members that are placed directly over the existing metal roof and are easily centered over the underlying purlins [Figure 11]. These additional structural members placed directly over the existing roof purlins may have the added advantage of increasing the load resistance and other performance characteristics. If properly accounted for in design and/or testing, this added strength can help offset increased loads when more recent codes govern the retrofit.
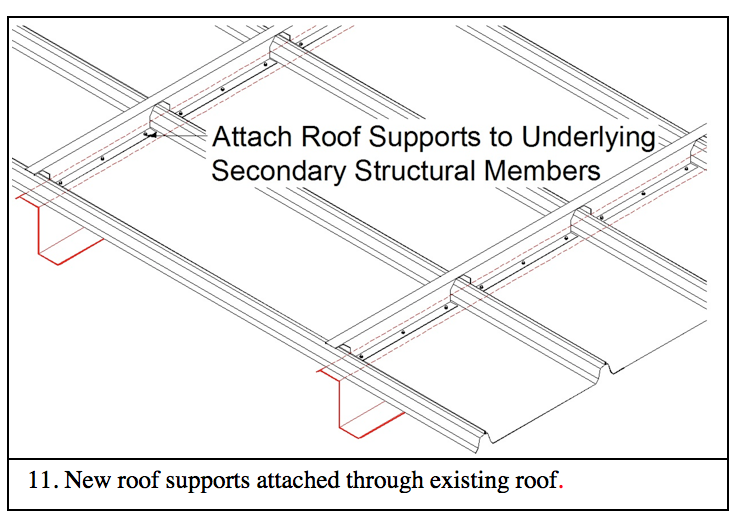
Single-ply roof systems typically have board insulation in-between the metal roof ribs and one, or more, layer(s) of insulation, or coverboard, on top of the first layer, which typically do not add structural capacity to the roof [Figure 12].
Most existing wind uplift ratings for membrane roofs are based on a 22 gauge, or thicker, steel deck with a 33 ksi yield strength. Some mechanically-fastened roof designs may require an 80 ksi deck yield strength instead of the 50 ksi yield strength often used for structural metal roofs in metal buildings. Most mechanically-attached single-ply roofs are required to be attached to underlying existing purlins [Figure 12] because the existing roof was not intended to support these concentrated loads.
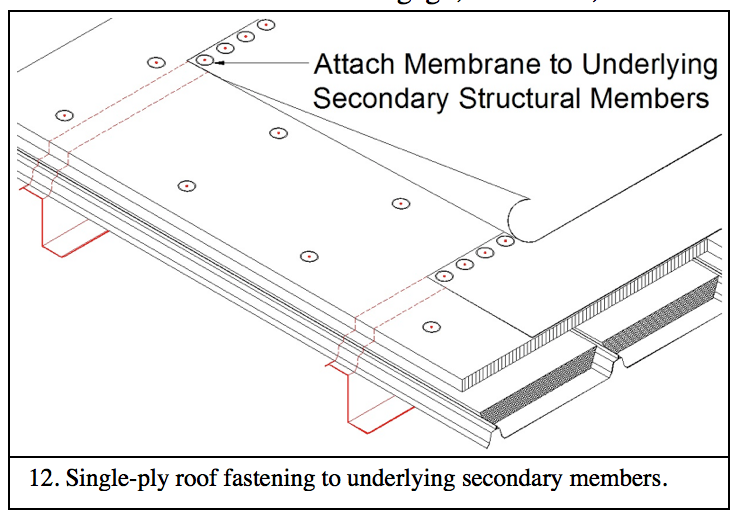
Mechanically-attached single-ply roof membranes are more difficult to attach to existing secondary structural members than metal over metal retrofits, as purlins are concealed below the insulation layers. This can become a significant issue in ensuring that the membrane is attached correctly during construction [Figure 12].
Metal building roofs are designed based on certain assumptions with regard to the load path and resisting the code specified loads. For a retrofit scenario using a single-ply membrane roof, not only is load path and strength/stiffness of the metal substrate different than typically assumed, but the loads are typically higher if compliance with a more recent code is required. Designers must develop an enhancement solution where existing purlins below the existing metal roof are spaced too far apart to achieve code compliance. Existing secondary structural members may require reinforcement at purlin laps and other structural modifications. One method to enhance an existing structure is to add secondary structural members underneath the existing metal roof. Unfortunately, adding these new members underneath the existing roof is expensive and disruptive to building operations.
Single-ply membrane retrofits are either mechanically-fastened or adhered to the existing structure. For an FM Global insured project, or a project that is required to meet FM Global recommendations by reference, the 2016 FM Global Data Sheet 1-31 may apply. Data Sheet 1-31, Section 2.2.4 indicates that only mechanically-fastened roofs that are attached into secondary structural members are permitted. This is presumably due to unknowns regarding the remaining structural capacity of the existing metal roof that will serve as a roof deck. Data Sheet 1-31, Section 3.1.3 recommends increasing insulation board fastening by 50 percent when attaching insulation board into less than a 22 gauge deck. Data Sheet 1-31, Section 3.1.4 recommends the single-ply membrane fastener density be increased by decreasing the space between fasteners where additional rows of fasteners are not practical due to the lack of secondary structural members. Decreasing fastener spacing will work to a certain point, but may not be sufficient in certain uplift zones.
It is recommended that a design review be performed of the retrofit roof field, perimeter, and corner zones to ensure that the fastening of the roof system is code compliant and to ensure that the existing structure is suitable to withstand the current required loads.Quality control should be implemented during construction to ensure that single-ply membrane fasteners driven through insulation board layer(s) are properly engaged into secondary structural members.
Drag Load
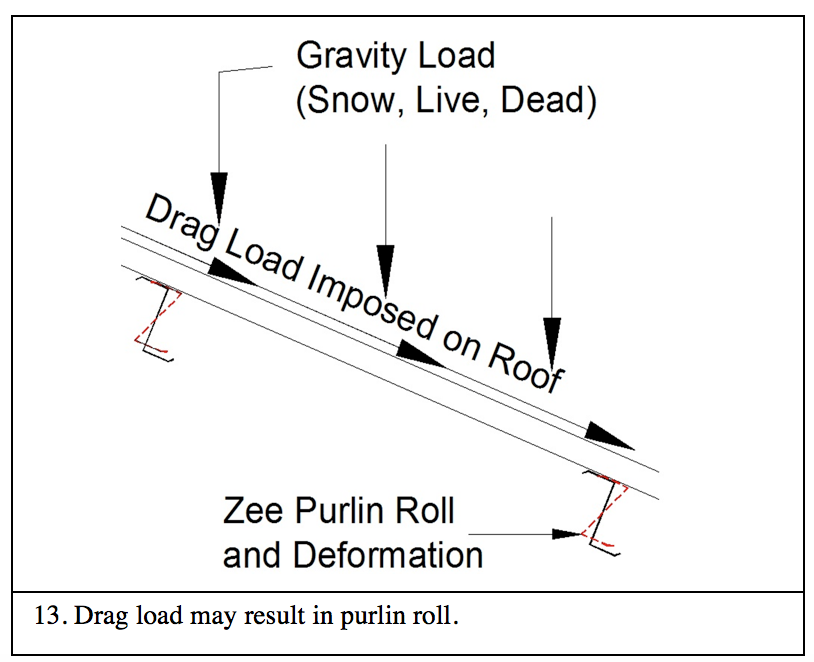
Drag load is a force that is the component of the gravity load parallel to the sloped roof surface, which has the effect of pulling the metal roof panels down the slope of the roof [Figure 13]. This load is particularly high on steeper slopes and when ice and snow accumulate on the roof.
Drag loads need to be resisted in a roof structure. In a metal roof, drag loads are resisted by mechanical anchorage of the metal roofing panels to the underlying structure. Drag load on roofs may result in purlin roll [Figure 13]. Excessive purlin roll, combined with sufficient gravity loads can result in structural collapse.
When metal roof retrofits are installed with secondary members placed over and anchored to the existing metal roof system, the secondary members provide the resistance to the drag forces. Existing secondary roof members can be restrained to resist increased drag loads with added bracing or flexural members. In the case of a single-ply retrofit, the loads are resisted by the lateral loading on long fasteners from the top of the insulating system to the existing purlins. The greater the insulation depth the greater the bending load on the fasteners. The fasteners should be evaluated for bending resistance.
It is recommended that a design review be performed by a licensed professional engineer to determine whether the anticipated system provides the necessary resistance to drag loads.
Fire Rating
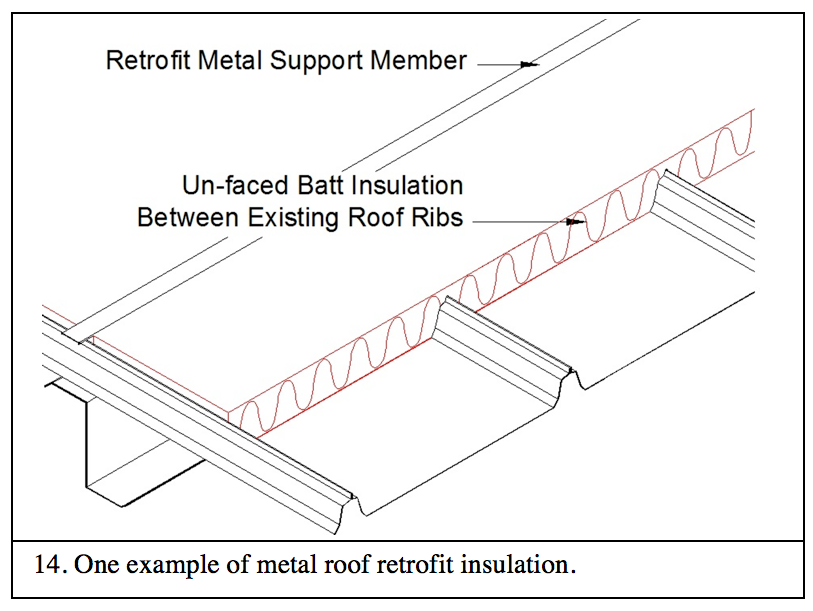
Both single-ply and metal retrofit roof systems can incorporate additional insulation between the new and old roofs. Un-faced fiberglass and other high melting point compressible insulation is typically utilized on metal roof retrofits [Figure 14], whereas single-ply roofs incorporate board insulation to provide a suitable bearing surface for a roof membrane [Figure 15]. Board insulation is usually a more efficient insulator than fiberglass batts. Metal panels are typically rated as a Class A roof assembly, according to IBC Section 1505.2, Exception 2, whereas single-ply membranes may or may not have a similar rating. Class A roof assemblies are those that are effective against severe fire test exposure, according to the IBC.
Board insulation used to support single-ply roofs is often expanded polystyrene cut to fit between existing metal roof ribs, combined with a top layer of either more insulation or a coverboard. The 2015 IBC, Section 2603 requires that direct to deck foam plastic insulation meet either UL 1256 or NFPA 276. An FM Global-insured project, or a project that is required to meet FM Global recommendations, would typically be required to meet the more conservative tests described in FM Standard 4880 or NFPA 276 to be an FM Class 1 rated roof assembly.
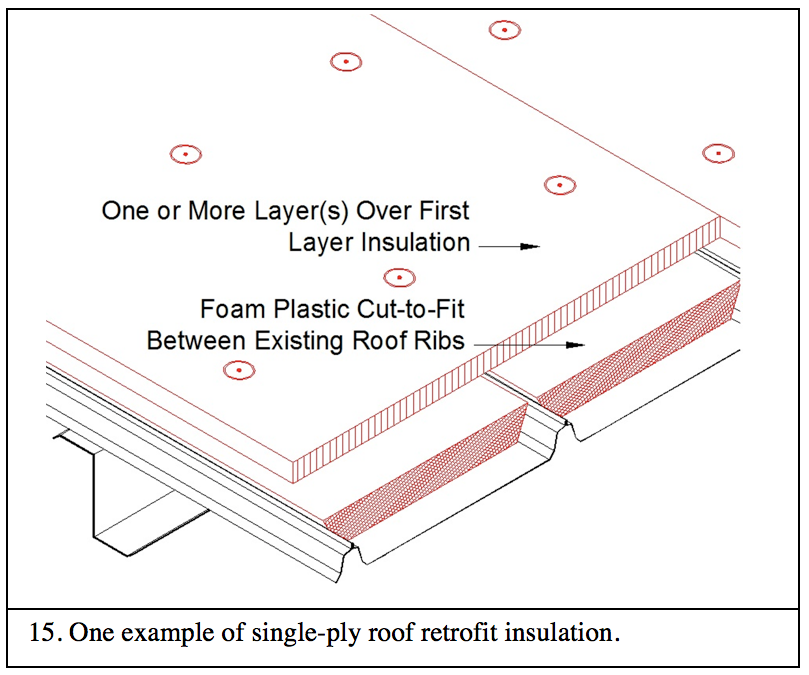
Un-faced fiberglass will typically pass both tests, whereas board insulation, especially the lower melt point expanded or extruded polystyrene, may not meet either standard. Some foam plastic insulation has been tested and passed the UL 1256 test when placed directly over a 22 gauge, or thicker, metal deck. As stated above, metal roofs have different properties than metal decks and may perform differently in these tests.
It is recommended that the roof designer verify the fire classification both above and below the retrofit roof system for building code and building insurer compliance for the retrofit roof system.
Summary
Retrofit roofs over existing metal roofs have several potential benefits. There are also several design considerations related to the decision to choose a metal, or single-ply roof, especially when retrofitting a metal building. The following recommendations are provided to assist with this decision:
Engage a licensed professional engineer practicing structural engineering with knowledge of metal buildings to evaluate the following:
4 Existing roof and structural system to ensure it is adequate for current building codes and to support the anticipated loads imposed by the retrofit roof system.
4 Retrofit roof field, perimeter, and corner zones to ensure code compliant fastening of the roof system.
4 Necessary resistance to anticipated drag loads on the retrofit roof system and existing structure.
The retrofit roof designer should verify the fire classification both above and below the retrofit roof system for building code compliance and building insurer acceptance for the retrofit roof system.
The following additional recommendations are specific to single-ply over metal roof retrofits:
Engage a licensed professional engineer practicing structural engineering with knowledge of metal buildings to evaluate the unbalanced loads and potential water accumulation on a single-ply retrofit roof with respect to structural capacity and drainage provisions.
Consult with the local building official, a licensed professional engineer practicing structural engineering, and the single-ply roof manufacturer to confirm that the existing building’s metal roof is adequate to perform as a structural deck for a non-metal sheeted roof.
Implement quality control during construction to ensure that single-ply membrane fasteners driven through insulation board layer(s) are properly engaged into secondary structural members.
Building owners, and their design professionals and contractors, should evaluate retrofit roof solutions for their project to determine what is the most prudent choice. MR